How does Sheffield Metals produce materials for customers?
Sheffield Metals International (SMI) is a leading provider of metal roofing materials, including metal coils, sheets, and accessories like clips and fasteners. We provide services for architects, contractors, and fabricators through our CAT (commercial, architectural and technical) team. Plus, we release weekly content like this article to provide additional education on a variety of topics.
We often get questions about how Sheffield stocks inventory and what role we play in the production process. While the gap between the steel mill and panel fabrication may seem small, it plays a significant role in getting our customers exactly what they need and keeping their businesses running efficiently. If you’re someone curious about how a metal roofing supplier operates and what our production process looks like, this article is for you.
In this article, we’ll look at Sheffield Metals’ production process and how coils and sheets are produced for customers.
How Does Production Work at Sheffield Metals?
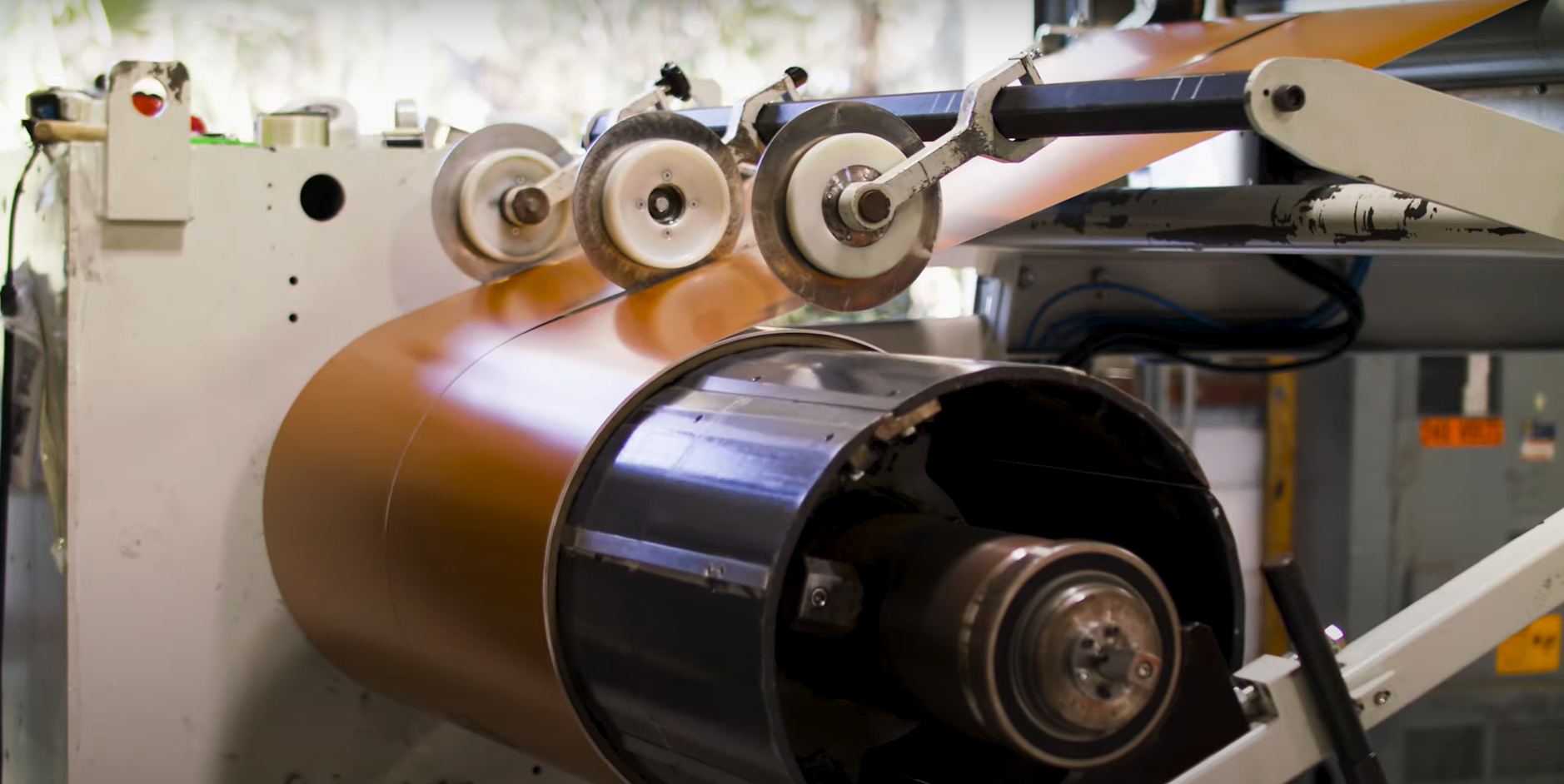
Before they get to production, Sheffield purchases coils from a steel mill. From there, the coils are sent to a paint coating line, and finally shipped to a Sheffield Metals facility to be cut to the customers’ desired width and length. The material is then organized into our inventory to await the production process.
Once the metal is in our building, our inside sales members will transfer orders to our production assistant. The assistant will choose what coils we have in stock that will work best to fulfill that order – typically, we’ll use coil that has been sitting in inventory, on a first-in, first-out basis, so our products stay fresh.
The cut-to-length and slitting line are where coils and sheets are produced to the customers requested specifications.
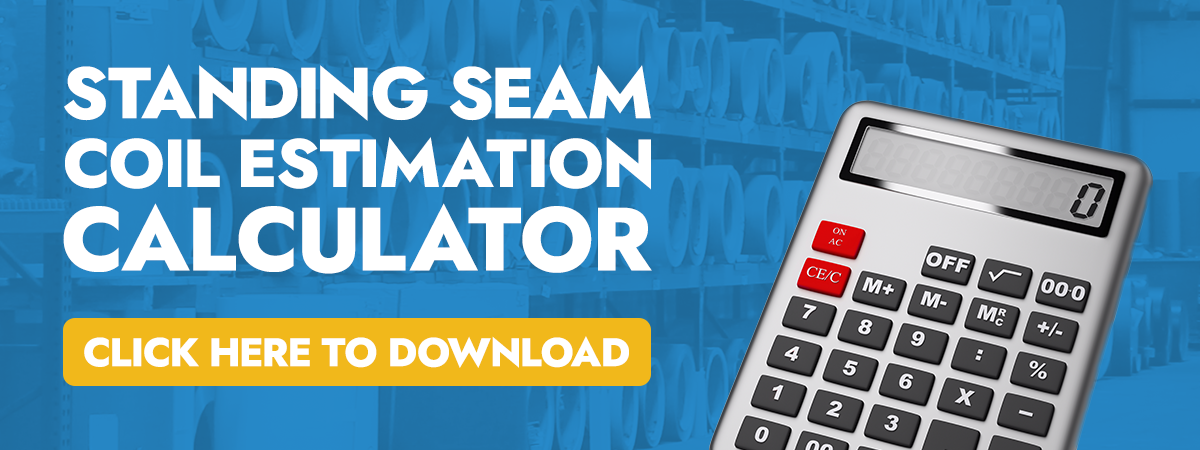
How Coils Are Slit to Width
The slitting line is where coils are cut to specified dimensions. This process takes the original coil, also known as the “master coil”, from the steel mill and transforms it into the workable materials used by metal roofing contractors and fabricators.
Once a new batch is ready for slitting, the operator will pull that material and prepare it by loading the master coil onto the machine, uncoiling it, running it through the slit head, and slitting it to the desired length. Most coils will be split in half.
Cardboard cores are placed onto the recoiler, which is used to hold the metal during transit. The metal slowly moves through the slitter and then is attached to these cores, then slit to the exact amount of material the customer requests.
After it’s run on the recoiler at the back end of the machine, it moves along to a spinning tree which can have two, three or sometimes four arms, based on the specific machine.
The coil is pushed into the tree and rotated. After that, it’s put onto a conveyer belt to get it ready for shipping. The slit coil is placed on a skid and banded down. A label and an outer layer of plastic wrap are added for protection during transit. Then it’s ready for shipping.
Standard Widths and Batching Orders
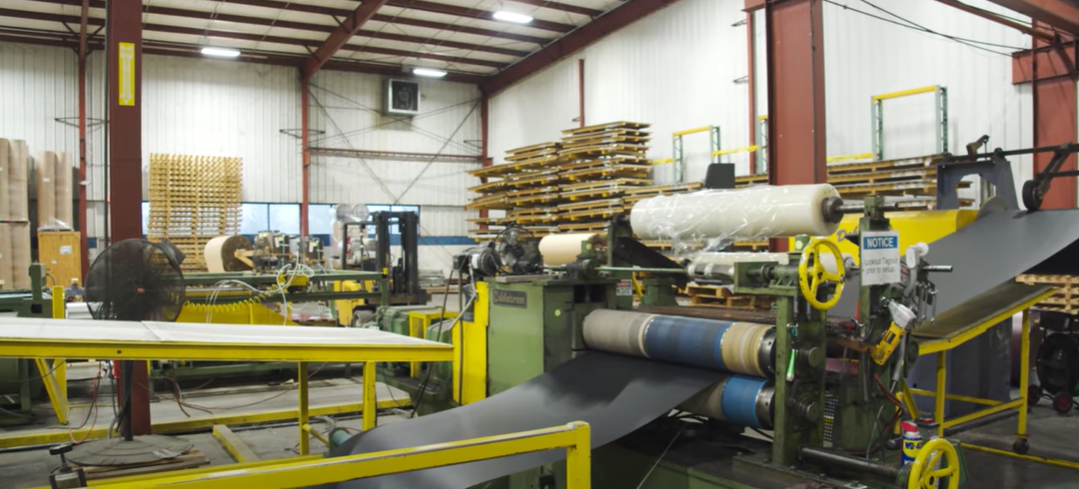
On the slitting line, metal coils are cut to standard widths – the most common cuts are 24”, 20”, and 16” from 40” and 48” master coils. These are the standard widths of master coils that Sheffield Metals keeps in stock.
The production assistant will decide the number of master coils needed for slitting based on the unique sales order – it’s up to them to schedule when each order will be produced, and how to batch them for optimal efficiency.
Similar orders will be batched together so that operators can stay in rhythm and maximize production throughout the day. For instance, all 24” coils would be cut on one day, 20” coils on another.
The operations team works hard to maximize efficiency by batching orders so customers can get their material as soon as possible.
Sheffield Metals slits all orders to custom lengths, but custom widths may incur additional setup and dropcut fees.
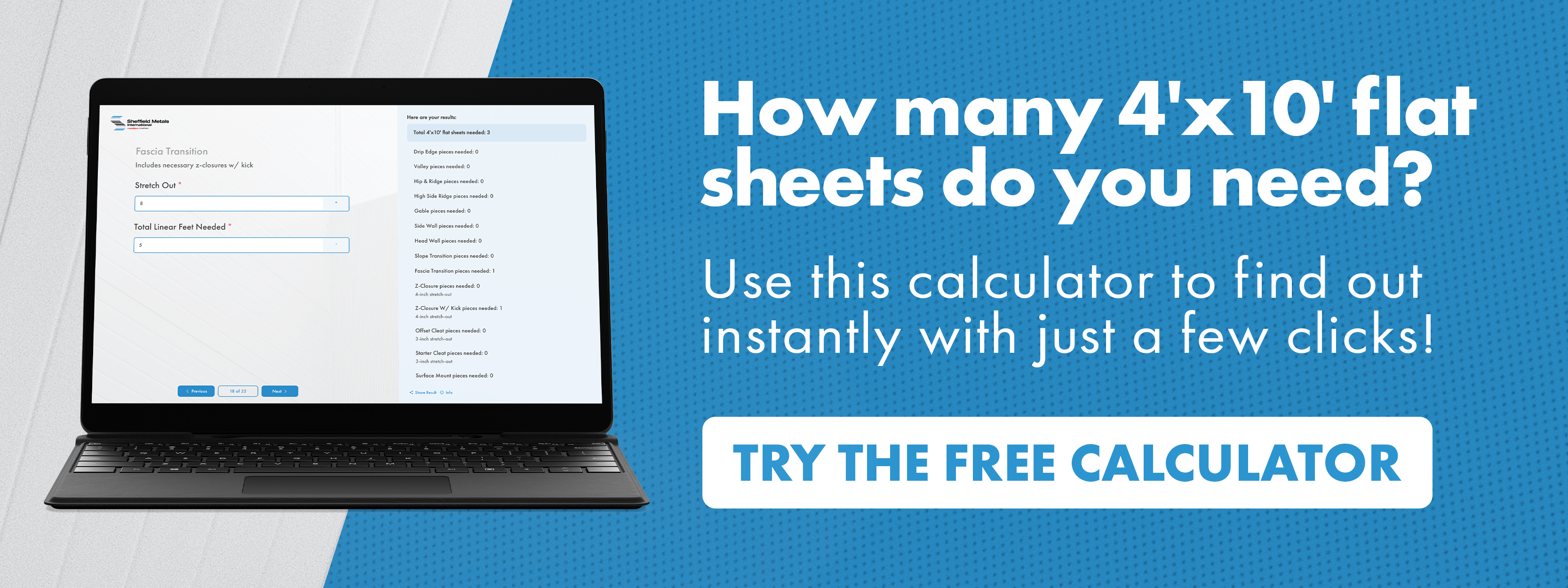
How Metal Sheets are Processed
The cut-to-length line, also known as the CTL line, is where metal sheets are produced. Flat sheets can then be purchased by contractors and fabricators and run through a rollforming machine to get the desired panels for their project.
The cut-to-length production line deals with leveling and cutting metal sheets to the desired lengths for customers. The material is fed through felt pads, which cleans the material of any lingering dirt and grime before it is unrolled by the CTL (cut-to-length) machine.
The material is then run through a flattening process which eliminates the “memory” of the sheets so that they remain flat without curling. The sheets are then cut to the standard or custom length.
These sheets are then transferred to the end of the machine, where they’re stacked in a pile.
Sheffield Metals’ standard sizes for sheets are 4’x10’. (48” x 120”)
The order process for both the slitting line and the cut-to-length line is similar – inside sales communicates the order to the production or operations assistant, who then chooses what material is going to be used.
Since the cut-to-length line deals with shorter amounts of materials, scheduling can be a bit less intensive than the slitting line.
Like the slitting line, Sheffield Metals can fulfill custom orders for a wide variety of dimensions and colors.
How is Quality Maintained on the Production Line?
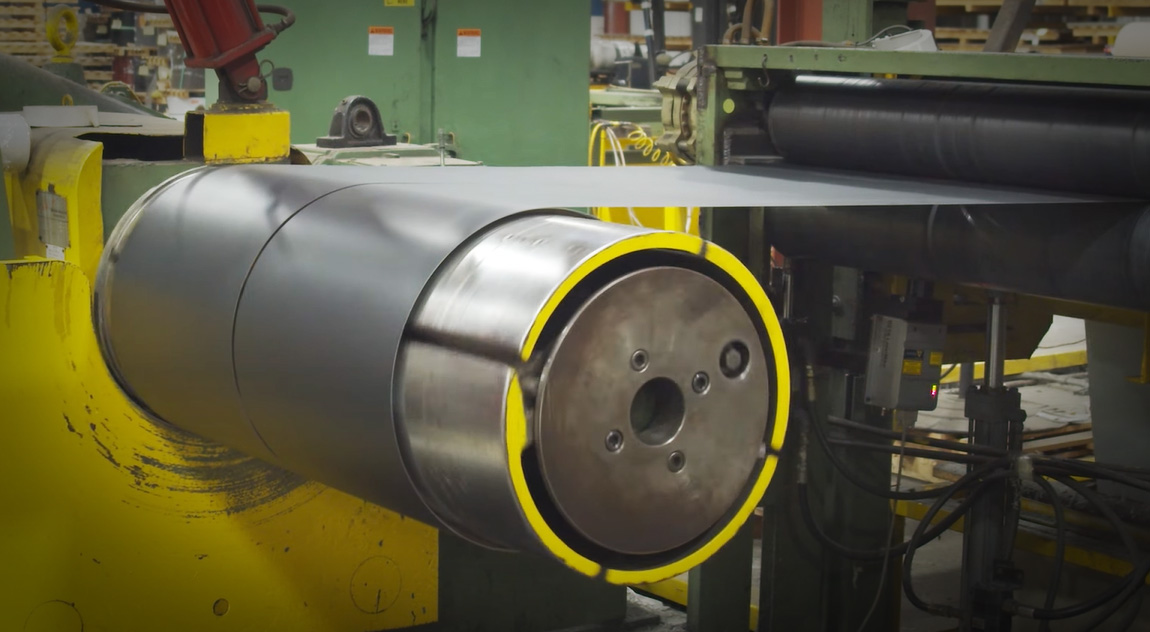
On both machines, there are felt pads which apply pressure to the material – these pads clean off the dust and dirt that may build up on the metal during shipments. It also helps the PVC film adhere better to the surface of the materials.
Sometimes, material is damaged in transit, leaving dents, dings, crushed edges, holes in the metal or water spots. In these cases, it’s up to the operator to spot that damage as it’s being run through the production line. Once damage is spotted, production is halted and it’s replaced with fresh material.
Our entire team is dedicated to ensuring you get high-quality material on time by focusing on streamlining our production process. We’re always seeking new ways to improve efficiency and serve our customers in the best way possible.
Need to Place an Order at Sheffield Metals?
There are many options when it comes to choosing a metal roofing supplier. The key is to find a reliable, trusted source in the industry with a proven track record of projects, references, and accompanying support that can provide assistance even after you purchase material.
At Sheffield Metals, we’re committed to helping our customers every step of the way, from their initial buying decision all the way through their finished project. Aside from offering metal sheet and coil and a variety of metal roofing accessories, we also provide technical assistance, including our engineered panel profiles complete with testing and warranty information.
Feel free to check out additional resources related to this topic below:
What to Expect When You Buy from Sheffield Metals – Sheffield Metals
Sheffield Metals Products, Processes and Services Overview – Sheffield Metals
Contact us today to place an order.
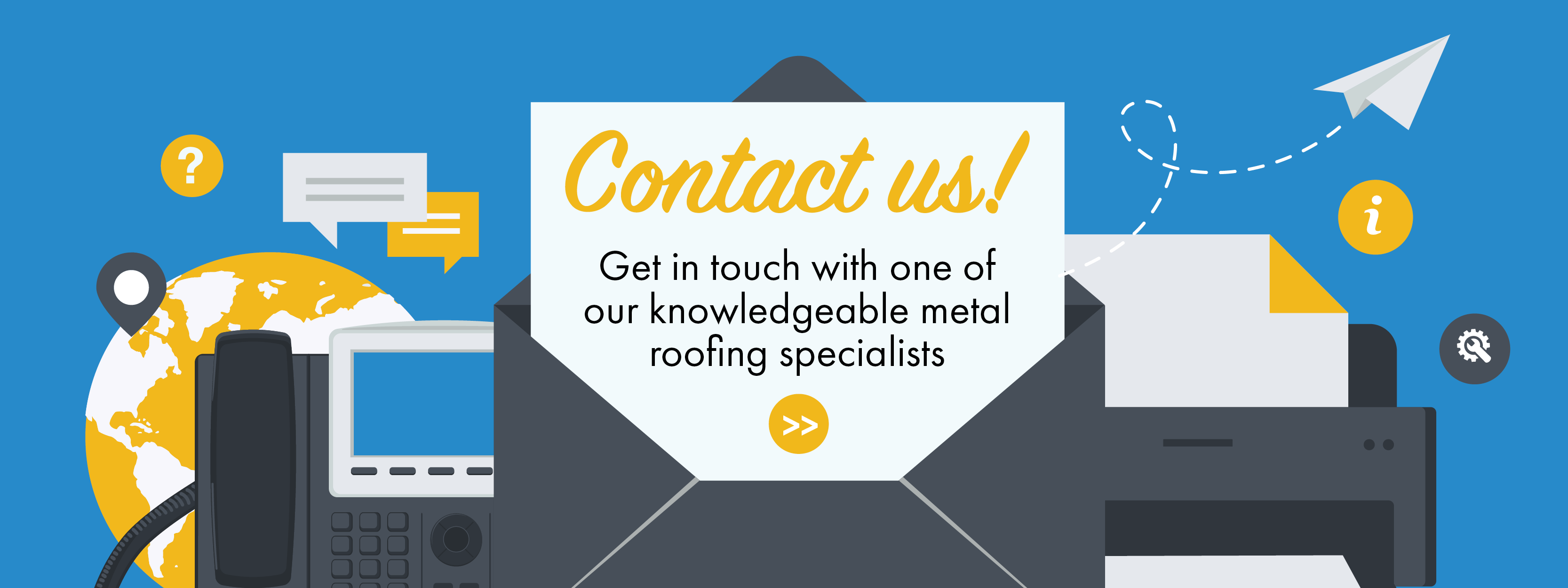