No matter what roof type you’re looking to purchase, it’s often the most critical question you ask: How much does it cost?
Here’s the short answer to that question: It depends.
We understand that might not be the answer you were looking for, but it’s true. No one type of metal roof costs the same as the next one, and we think it would be unfair to lump all different options together under one price. Instead, we want to give you an accurate and thorough explanation of:
- What factors into the cost of a metal roof?
- What product do specifications affect the price of a metal roof?
- What is the cost of a metal roof in 2022?
At Sheffield Metals, we’ve spent over 20 years helping property owners purchase the metal roof that best fits their budgets and needs. We know how important it is for you to price out a metal roof that you feel comfortable with, so we want to help equip you with the information you need to make an informed purchase.
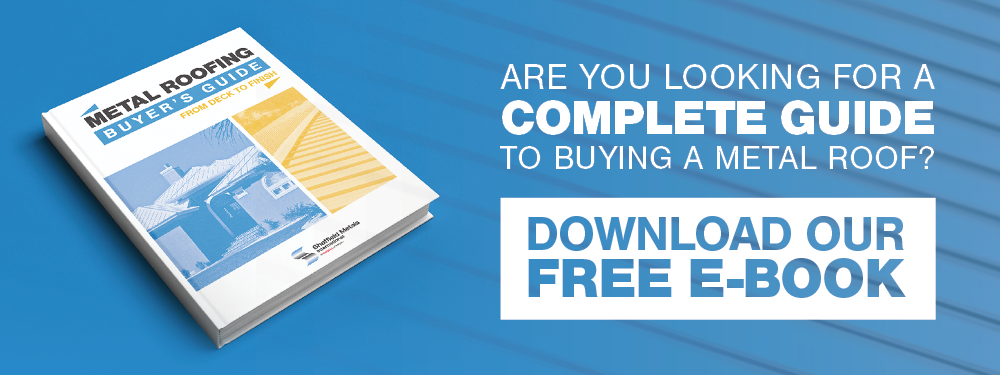
What Factors Into the Cost of a Metal Roof?
Understanding the different variables that factor into the cost of a metal roof will help you better determine what type or style of metal roof is the best choice for you or one of your clients. To better understand where your money goes when you purchase a metal roof, we’ve broken it down into three separate costs:
- Cost of materials
- Cost of labor
- Operating costs
Cost of Materials
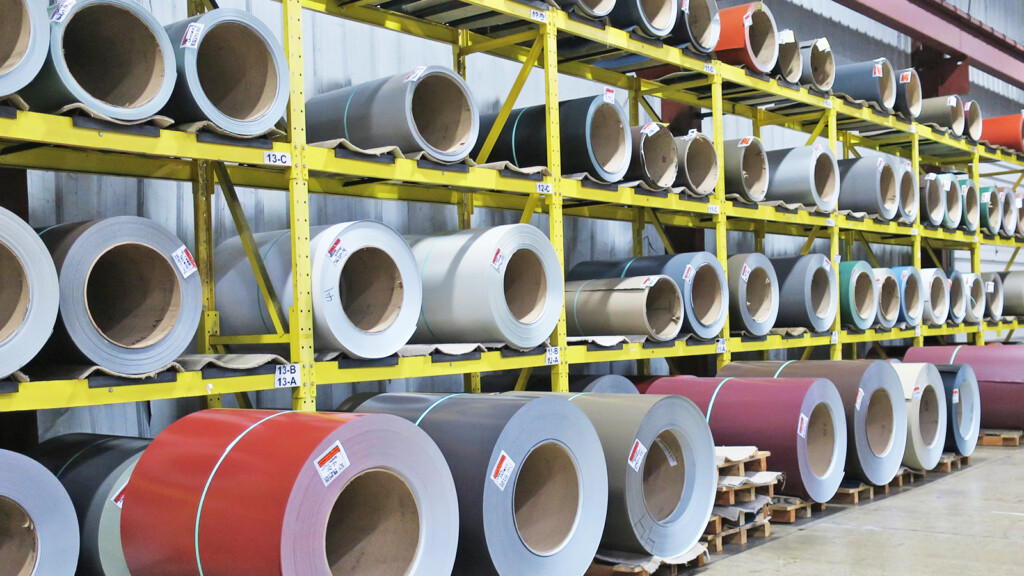
The cost of materials required for a project accounts for roughly 1/3 of the total price to install a metal roof. This part of the overall cost accounts for:
- Metal panels/profiles
- Flashings
- Underlayment
- Accessories (such as clips, fasteners, rivets, and sealant)
- Other miscellaneous materials that might be needed to complete an install
Cost of Labor
Accounting for another 1/3 of the price of a metal roof is how much the contractor charges for the actual installation portion of the project. Here’s a list of the breakdown to better understand what the cost of labor covers:
- Number of hours required to complete the project
- Wages and salaries of contractor’s employees
- Benefits and insurance for employees
- Payroll taxes paid by the contracting company
These factors are not always concrete and can vary based on the structure of a business, how long the project will take, and the complexity of the installation.
In 2022, inflation is on the rise in the U.S. and beyond (7-10% in some areas), which has directly influenced the cost of labor. If employers keep up with inflation to remain competitive and profitable, labor alone could cost 20% more than it did a year ago.
Operating Costs
Finally, the last 1/3 of the cost is comprised of the operating costs that help keep the company in business and functioning in the market. For a metal roof install, this part of the cost could help cover:
- Rent or utilities of a building or office space used
- Plus office supplies, internet, phones, etc.
- Advertising and promotion
- Vehicles and trailers needed to haul employees and materials
- Plus fuel, vehicle insurance, etc.
- Equipment or machinery used to rollform, cut, and seam panels
- Licensing and training required by industry or government
- Insurance
- Plus coverage for potential damages not covered by insurance
- Taxes
- Other day-to-day miscellaneous tools and items
No two businesses operate the same or require the same amount of money to function, which means there could be dramatic differences in operating costs from contractor to contractor.
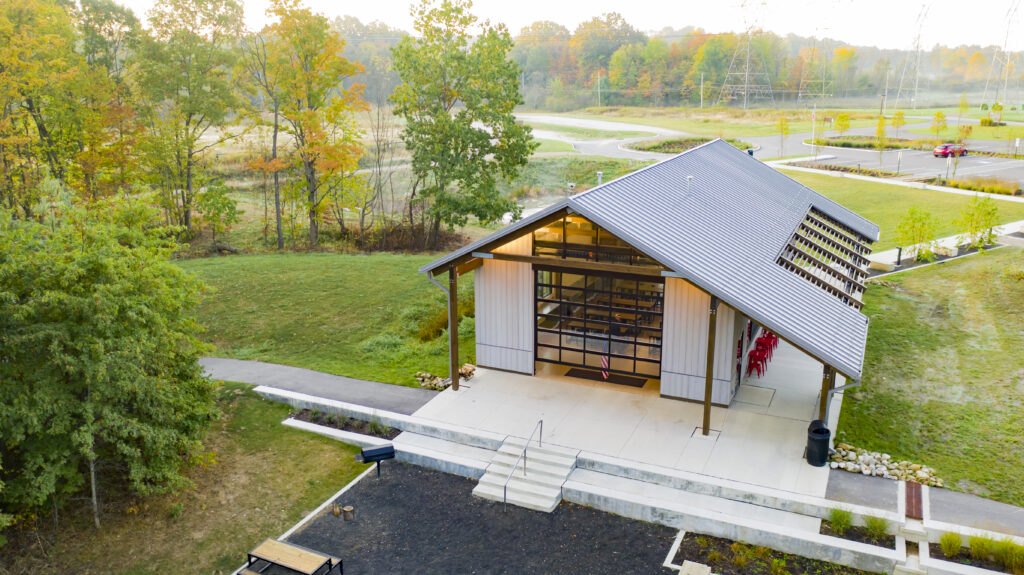
What Specifications Affect the Cost of a Metal Roof?
What else factors into the cost of a metal roof? Many of the pricing differences come down to a number of key specifications, including:
- Roof size
- Residential vs. commercial
- Type of metal material
- Order specifics
- Width
- Gauge
- Color
- Paint type
- Seam type
- Accessories
- Flashings
- Location or where you live
- Customizations
Roof Size
As you could probably already guess, the cost to complete a roofing job varies depending on the size of the roof (measured in square feet). If you need help calculating the square footage of your pitched roof, which is different from the flat base area of a home, follow these instructions:
- Find out the base area, or the area of land, that the building or home covers.
- If you have a property with numerous complex shapes, determine the area of the individual shapes and then add them together.
- Also, if you know you have a two-story property at 2,400 square feet, you would only use the square feet of one level (1,200 square feet).
- Determine your roof pitch, or how much the roof rises over 12 inches. For example, if your roof rises 8 inches for every 12 inches, the roof pitch is 8/12. Here’s a photo for reference:
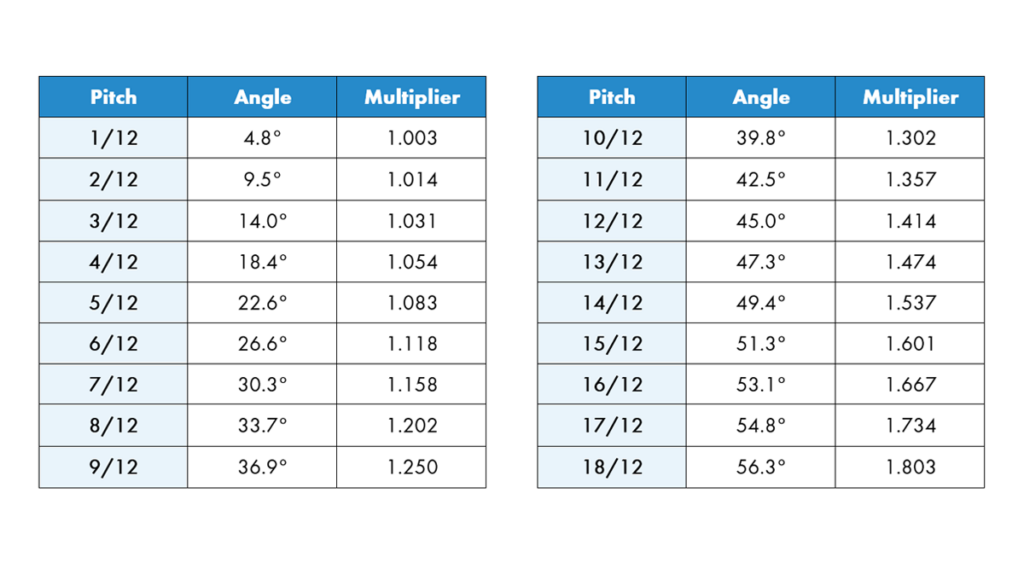
- From there, multiply the area by the typical slope correction values (these may vary slightly between manufacturers but still offers an approximate square foot value) shown in the chart.
- For example: If you have an 8/12 roof pitch and a 1,200 square foot base area, you would reference the multiplier in the chart for that pitch, or 1.202, and use this formula:
Square foot base area x Roof pitch multiplier = Roofing square feet
1,200 (square feet) x 1.202 = 1,442.4 roofing square feet
Commercial or Residential Project
Typically, commercial metal roofing projects tend to cost more than residential ones because more materials, time, technique, and labor are required on commercial buildings.
Metal Material Type
The type of metal material makes a difference in the final price, as some metals come at a higher cost and some cost significantly less. We’ll focus on the six most common metal materials: bare Galvalume, painted Galvalume, aluminum, stainless steel, copper, and zinc.
Here are average price ranges for just the coil; these numbers do NOT account for installation, other thicknesses, finishes, colors, locations, or special orders:
Bare Galvalume, Galvalume Plus, or acrylic-coated Galvalume (24-gauge) | $1.25 to $1.85 per square foot |
Painted Galvalume (24-gauge) | $1.75 to $2.35 per square foot |
Painted aluminum (.032” to .040”) | $2.20 to $2.80 per square foot |
Stainless steel (.015” to .024”) | $5.00 to $10.00 per square foot |
Copper (16-oz to 24-oz) | $8.50 to $10.50 per pound |
Zinc (.7 mm to 1.5 mm) | $6.00 to $9.00 per pound |
The cost ranges differ from one another for several reasons, such as:
- Premium materials
- All metals used in metal roofing are viable options for home or building owners, but some are stronger than others or carry specialized qualities that put them at a higher price. For example, copper and zinc develop a protective covering called patina over time that further resists corrosion, which is one reason why both of these materials cost more.
- Market price
- All of the metals above are commodities, meaning they go up and down according to the selling price in a given market.
- In 2021 and 2022, steel and aluminum are experiencing price increases and extreme market volatility. Learn more about the steel market’s recent pricing and supply challenges here.
- Availability
- For example, steel is a standard alloy produced and used in infrastructure and construction, so it’s accessible and readily available for companies to purchase from domestic or foreign steel manufacturers. The same goes for aluminum, which is the 3rd most abundant metal in the earth’s crust by making up about 8.1% of it.
- On the other hand, copper makes up less than 0.0007% of the earth’s crust, so it makes sense that it comes at a much higher price when compared to other materials.
- Quantity
- The limited availability means the amount produced by manufacturers is less. So, some manufacturers might not even carry zinc or copper options, which is another factor affecting the price.
Order & Product Specifics
An attractive feature of metal roofing is the number of options available for buyers to choose from. At the same time, a number of these options on a quote or order can cause the price to fluctuate in either direction.
Width
Metal coil and sheets typically come in many different standard widths (anywhere from 48’’ to 16”) that manufacturers will cut to with no extra charge. If a customer or buyer needs the coil or sheets in a non-standard or customized width, it could lead to a higher price.
Gauge
The gauge or thickness of the metal factors into the cost. The thicker the metal is, the higher the price will be.
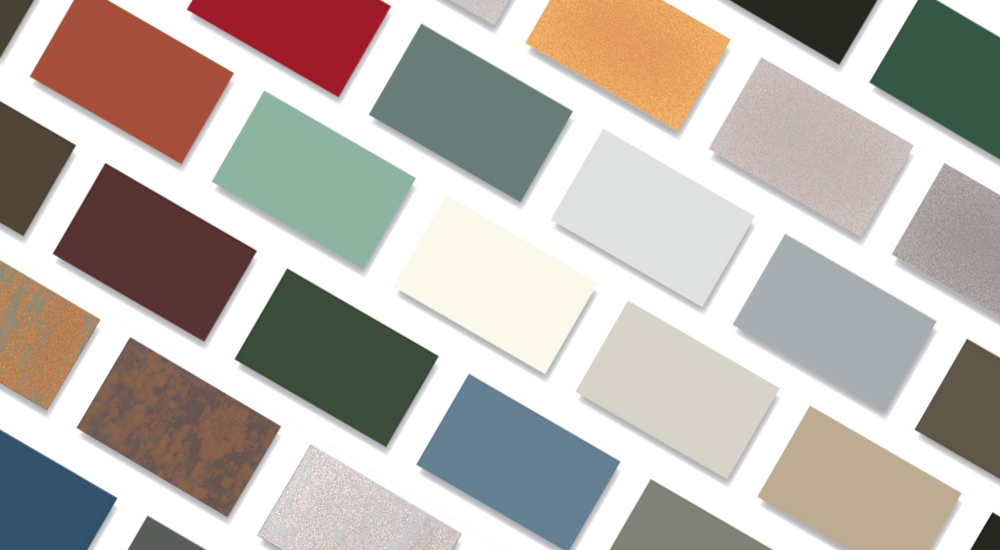
Color
Have you ever been to a car dealership and noticed that some cars are more expensive just because of the color? This same concept applies to metal roofing. Some colors are harder for paint companies to develop, some require extra materials to be added, and some might need one or more layers, all of which can increase the price.
For example, at Sheffield Metals, we have five different price levels that apply to our standard 24-gauge PVDF products:
- Unpainted Galvalume Plus (lowest)
- Standard
- Premium
- Metallic
- Weathered (highest)
Paint Type
Going along with the paint color is the type of paint system used to coat the coil, which can swing the price in both directions:
- Fluoroethylene vinyl ether (FEVE) – FEVE resins are made of various vinyl ether and fluoro-olefin units and are some of the most expensive paint systems in standing seam metal roofing.
- Polyvinylidene fluoride (PVDF) – This resin is comprised of about 70% PVDF and 30% acrylic. Commonly referred to as Kynar 500® or Hylar 5000®, PVDF resins are some of the best protective coatings available and tend to cost more than SMPs and less than FEVEs.
- Silicone-modified polyester (SMP) – SMP coatings, a combination mixture of polyester and silicone materials, are a step below PVDF. SMPs offer great protection, though not as well as PVDF, and come at a lower price.
- Polyester – While polyester (a synthetic polymer) is not the best resin to protect against chalking or fading, it comes at the lowest price point.
Seam Type
There are essentially four general seam types used to connect panels in metal roofing:
- Snap-lock
- Mechanical
- Tee/batten panel
- Nail flange or fastener flange
Of the four, snap-lock and lap seams are the easiest to install. With a snap-lock system, the panel edges are rollformed to snap together without any mechanical seaming, which cuts down on labor and keeps costs lower. With lap seams, the ends of the panels aren’t truly ever connected together, as the edges overlap and are then fastened to the deck through the top of the panel.
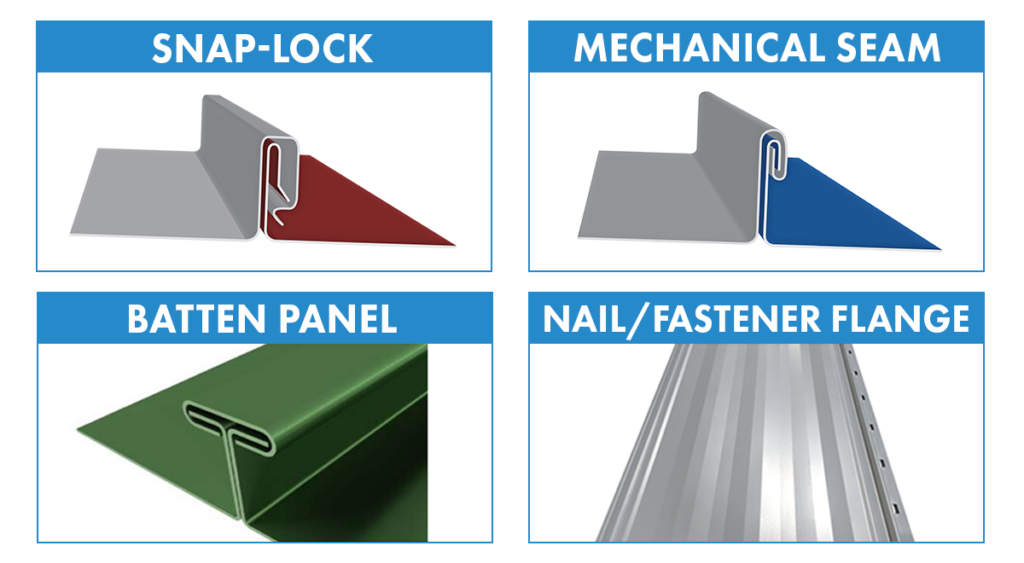
The more labor-intensive and expensive seam options are mechanical or tee seams. Both of these require a hand or robotic seamer that bend the edges to lock the panels together.
Accessories
Accessories are the pieces and parts needed to ensure the metal roof performs to the best of its ability. There are numerous different options for most accessories, making the cost go up or down depending on the type. Here’s a quick run-down of the different types and if one option is more expensive:
- Clips
- Engineered clips (more expensive)
- Non-engineered clips
- Fasteners, screws, and rivets
- Underlayment
- Mechanically attached synthetic underlayment
- Fully-adhered peel and stick
- Ice and water shield (most expensive)
- Clamps, snow-retention systems, and other attachment solutions
- Sealant and butyl tape
- Paint pens and touch-up paint
Flashings / Penetration Zones
Another factor affecting the cost is the number of flashing zones and penetration points on a roof. To distinguish between the two, just know that all penetration points are flashing zones, but not all flashing zones are penetration points:
- Flashing zone – A spot on the roof where extra materials like sheet metal or rubber are added to provide extra weather-tightness. Flashing materials are typically required at valleys, chimneys, skylights, and other cuts in the roof.
- Penetration points – A point on the roof where something is coming through the metal. This includes vents, pipes, or chimneys. Many manufacturers require pre-welded curbs to be installed at non-round penetrations for weathertight warranty applications.
These scenarios require installers to make extra precision cuts in the materials or install additional materials, such as a pipe boot, sheet metal, etc. These added materials can drive up the cost of a metal roof.
Project Location
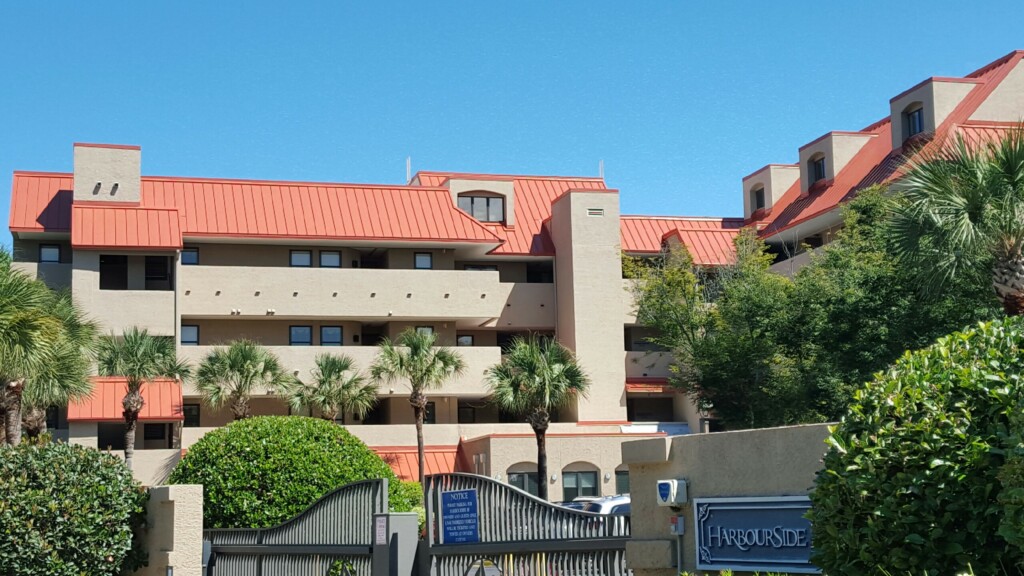
You might be asking yourself: Why would the cost of a metal roof change by location?
Just like property costs change depending on the city, state, or even the country — not every product costs the same everywhere you go. That being said, here are a few factors that weigh into why a metal roof might be higher or lower depending on your location:
- The overall cost of living
- For example, products and services cost more in New York City or Los Angeles because living costs are higher.
- The cost of labor
- Union labor: More expensive, but typically have a higher emphasis on training.
- Non-union labor: Less expensive, potentially less-trained workers.
- There is no concrete evidence that union or non-union contractors are better than the other, so just do your research and ask for referrals ahead of time to avoid any potential metal roof problems.
- The prominent regional manufacturers in the area
- Quantity of portable rollformers in the region
- Where the materials are coming from
- For example, most steel mills are located on or near the east coast of the U.S. If you live on the west coast, it could cost more because the coils/sheets require additional shipping.
Customization(s)
Like most products, customization typically comes at a cost. This includes:
- Custom colors
- The cost of a custom color varies by color choice and quantity. For example, custom earth-tone colors come at a price premium, but not as much as a non-standard, vivid custom color. Brighter custom colors experience the highest price jump because they require more pigments and are more challenging to produce.
- Note: Ask a manufacturer about their custom color quantity minimums and if they limit their paint warranties for custom colors.
- Custom flashings
- An additional fee could be charged if specialized flashing materials like customized pipe boots or valley flashings are required.
Metal Roof Cost Examples [2022 Prices]
The best way for us to explain how much an actual metal roof will cost is to give the quoted prices of real metal roofing projects that have been completed. Keep in mind that these prices capture one project based on its specifications.
While these price ranges are good representations of the cost of a metal roof installation, prices will still vary depending on:
- Coil/metal type
- Size/specifications
- Roof geometries
- Profile or seam type
- Geographic location (cost of living)
- Residential vs. commercial
- Accessories
- Colors and finishes
- Engineering requirements
Snap-Lock Metal Roof Price Examples in 2022
Quote from Ohio Contractor:
Coil type | 24-gauge Galvalume with PVDF finish |
Profile | SMI 1.5 Snap-Lock 450 |
Color | Standard |
Structure size | 3,100 square feet |
Location | Midwestern U.S. – Ohio |
Actual quoted price | $21,700 total or approximately $7.00 per square foot |
Quote from Texas Contractor:
Coil type | 24-gauge Galvalume with PVDF finish |
Profile | SMI 1.5 Snap-Lock 450 |
Color | Standard |
Structure size | 3,100 square feet |
Location | Southwest U.S. – Texas |
Actual quoted price | $26,350 total or approximately $8.50 per square foot |
For the SMI 1.5″ Snap-Lock 450 profile, you can expect to pay anywhere from $7.00 to $11.50 per square foot.
(Note: These prices can fluctuate based on any combination of the conditions listed above.)
Mechanical Seam Metal Roof Price Examples in 2022
Quote from Ohio Contractor:
Coil type | 24-gauge Galvalume with PVDF finish |
Profile | SMI 1.5 Mechanical Seam |
Color | Standard |
Structure size | 3,100 square feet |
Location | Midwestern U.S. – Ohio |
Actual quoted price | $24,800 total or approximately $8.00 per square foot |
Quote from Texas Contractor:
Coil type | 24-gauge Galvalume with PVDF finish |
Profile | SMI 1.5 Mechanical Seam |
Color | Standard |
Structure size | 3,100 square feet |
Location | Southwest U.S. – Texas |
Actual quoted price | $31,000 total or approximately $10.00 per square foot |
For the SMI 1.5″ Mechanical Seam profile, you can expect to pay anywhere from $7.50 to $13.00 per square foot.
(Note: These prices can fluctuate based on any combination of the conditions listed above.)
Exposed Fastener Metal Roof Price Examples in 2022
Quote from Ohio Contractor:
Coil type | 29-gauge Galvalume with SMP finish |
Profile | Classic rib (exposed fastener) |
Color | Standard |
Structure size | 3,100 square feet |
Location | Midwestern U.S. – Ohio |
Actual quoted price | $15,500 total or approximately $5.00 per square foot |
Quote from Texas Contractor:
Coil type | 29-gauge Galvalume with SMP finish |
Profile | Classic rib (exposed fastener) |
Color | Standard |
Structure size | 3,100 square feet |
Location | Southwest U.S. – Texas |
Actual quoted price | $20,150 total or approximately $6.50 per square foot |
For a classic rib exposed fastener metal roof, you can expect to pay anywhere from $4.00 to $9.00 per square foot.
(Note: These prices can fluctuate based on any combination of the conditions listed above.)
Final Thoughts on the Cost of a Metal Roof
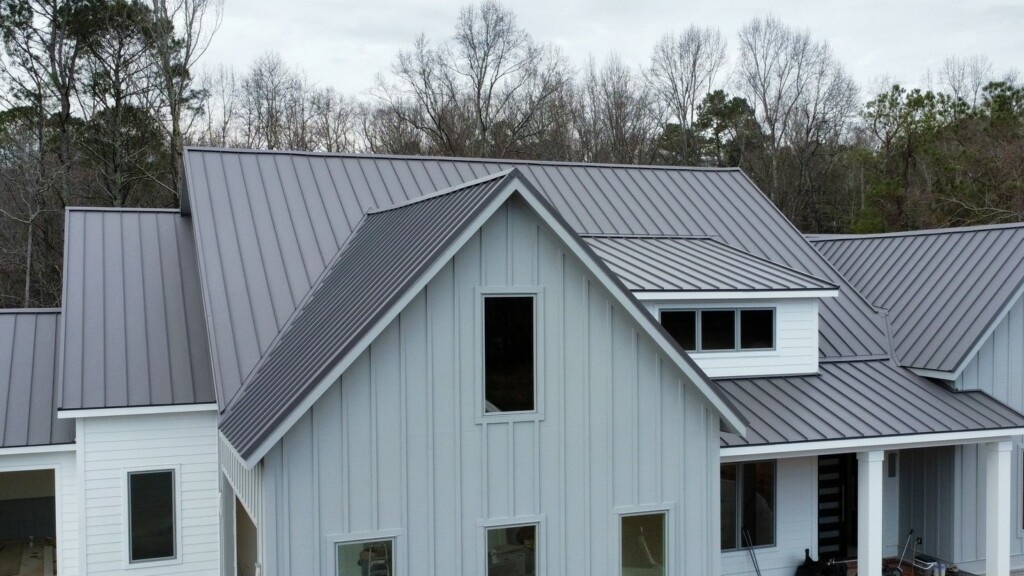
There are a lot of factors that affect the cost of a metal roof, so we understand that it can be overwhelming at times.
The best advice we can give you is this: Be realistic and keep your budget in mind. You always want to get the most out of your money, but you also don’t want to spend money you don’t have, so set a price and stick to it.
Remember, if you ever want to know more about what goes into the cost of a metal roof, talk to the manufacturer you’re purchasing from. They will be able to shed light on why one or more options could alter the cost.
At Sheffield Metals, we are here to answer your questions and help you choose the best metal roof that fits your budget. Or, if you’re looking for a contractor referral in your region, our team has an expansive network of contacts across the United States to help assist you.
Contact us today to schedule a consultation or speak with one of our knowledgeable metal roofing experts!
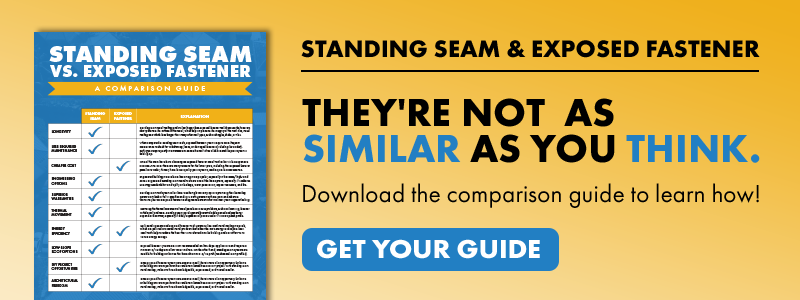