“This project was brought to us by a local roofer, Avery Roofing. It has six radiuses within the curve of the roof. The panels are approximately 76’ long around the roof. The building design is very unique, and not a lot of people were interested in taking on this job, so it’s one we wanted to take.”
-Joe Keene, Metal Roofing Contractor from Integrity Metals
An architectural standing seam metal roofing project located in Longboat Key, Florida, presented a unique challenge on a residential home situated between the Gulf of Mexico and the Intercoastal Waterway. The project was taken on by Integrity Metals, who utilized Sheffield Metals and New Tech Machinery products to bring the design to life.
Integrity Metals needed a trusted partner that could provide quality materials, plus the right engineered systems to contend with the region’s local codes and extreme weather.
In this case study, we’ll look at what specific obstacles Integrity Metals faced when working on this project, and how they worked with Sheffield Metals to find solutions.
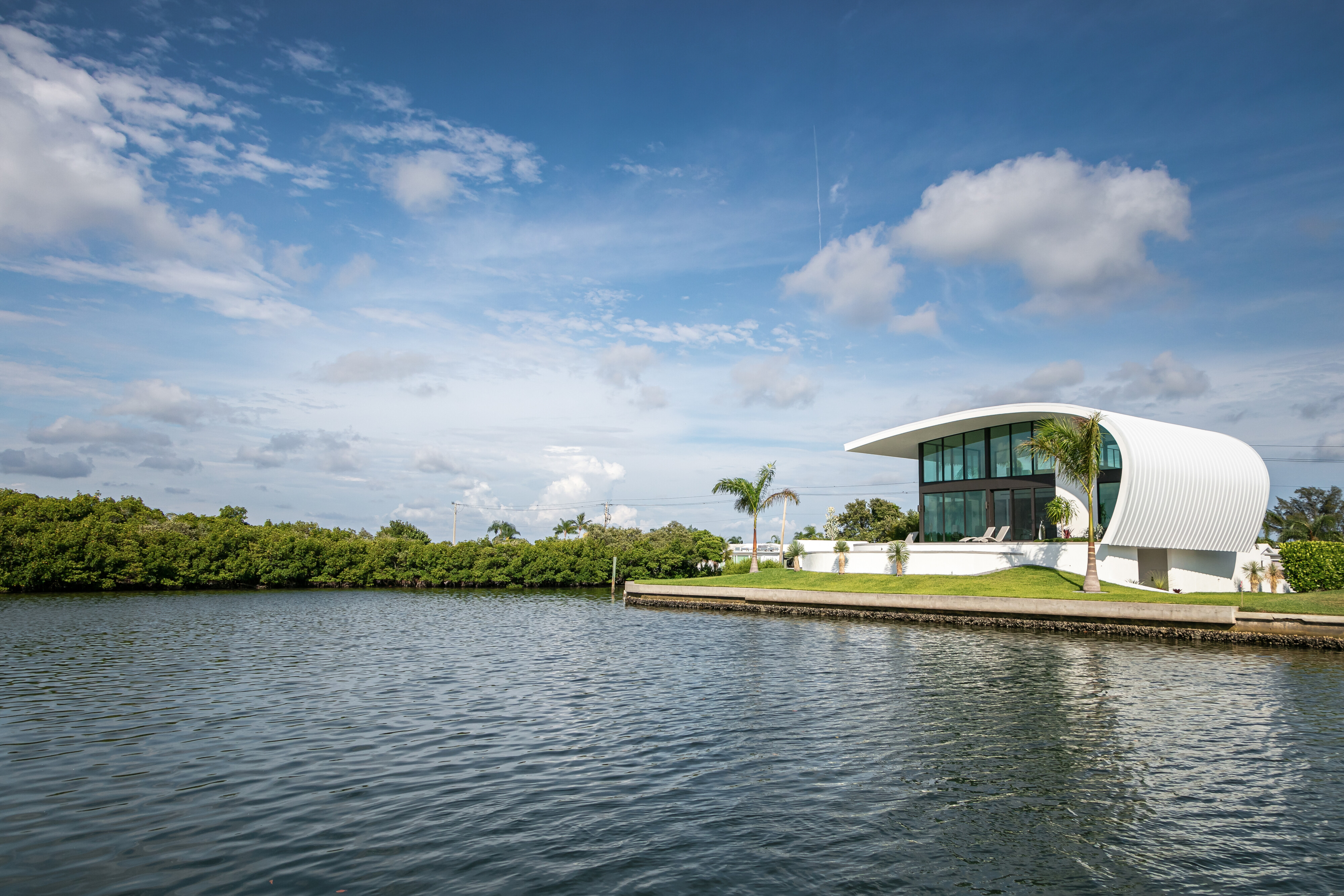
Key Project Aspects:
- Location: Longboat Key, Florida
- Customer profile: Homeowner
- Challenges: Radius roof design and regional conditions
- Contractor: Integrity Metals
- Metal Supplier: Sheffield Metals
What Were the Core Challenges for this Project?
1. Specialty Design
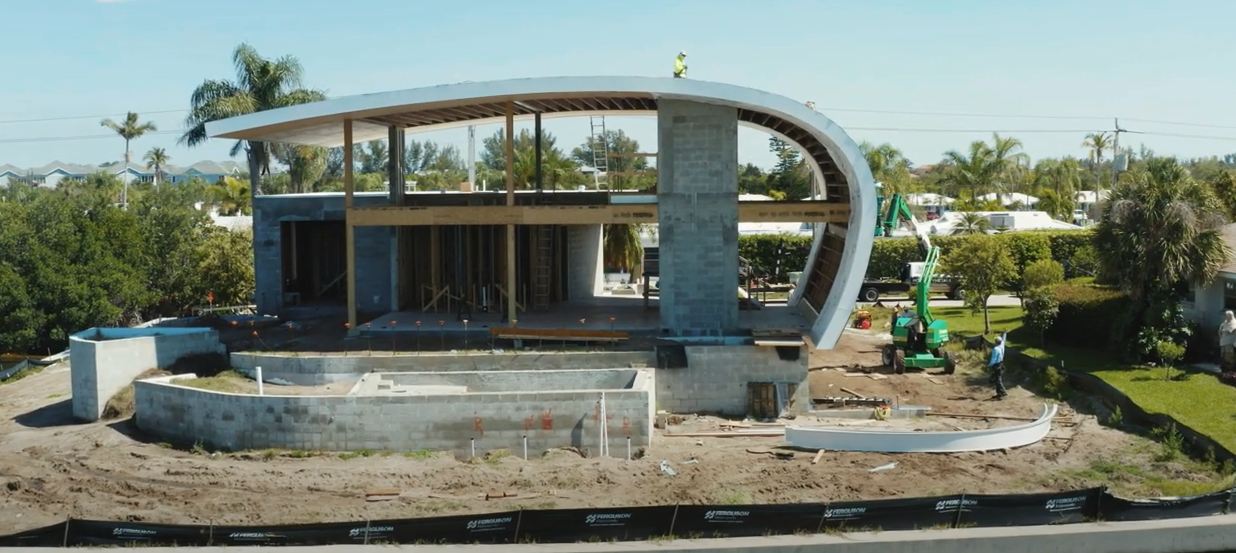
The radius roof featured a curved design with six different radiuses ranging from 212’ to 8’. Panels would be approximately 76’ long. The team was also located 200 miles from the jobsite, so getting the right materials and staying efficient was crucial.
To get the curvature right, precise calculations would be needed, along with a strategy to bend the metal without undermining its functionality. Unique roofing details would also be required, as the curving nature of the roof would be unlike a normal slope.
The team who took on the project would need to be flexible, well-versed in metal roof designs, and ready to solve issues when they arose.
2. Saltwater Corrosion
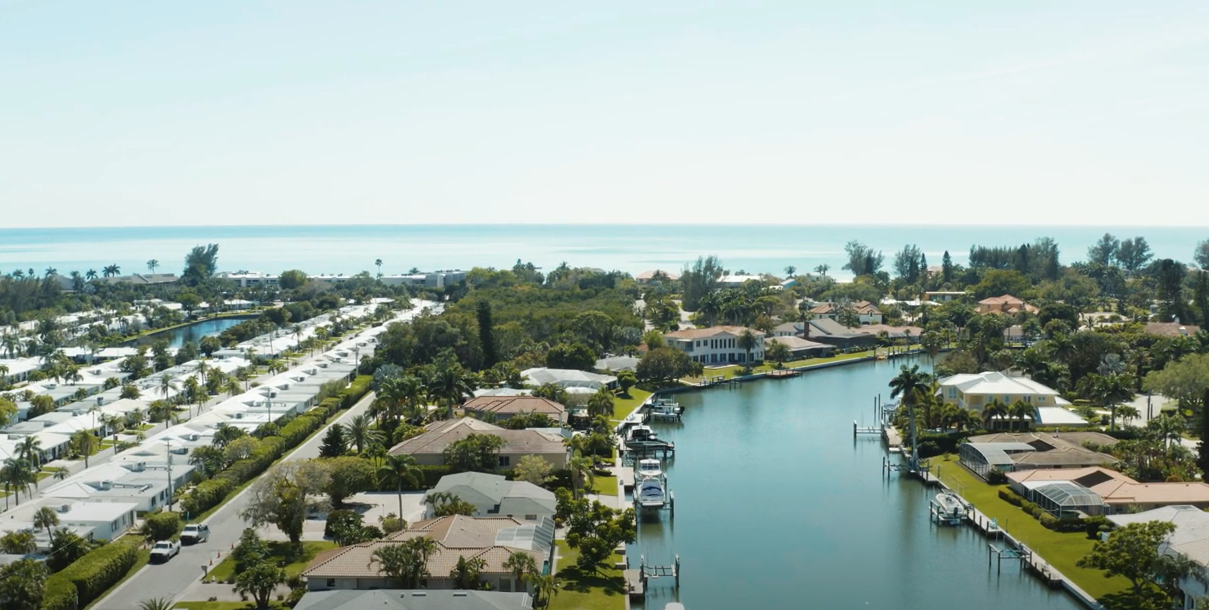
Longboat Key is a small slice of land floating between the Gulf of Mexico and Intercoastal Waterway, about halfway down the Florida peninsula. Its beautiful views and coastal breezes made it the perfect spot for a new home, but it presented a fresh set of challenges for the radius roof design.
Since the roof wouldn’t be further than 200 yards from the ocean, it would be in a prime spot to be affected by saltwater corrosion, which can start acting on metal roofs quickly, causing them to rust and break down, affecting their performance.
3. Wind Exposure
The radius roof was in the highest wind exposure category: Category D. Exposure categories are determined by where a specific structure is located and what other structures are around it to protect it from straight-line winds.
Buildings in urban areas are typically in the Exposure B category, as they have many other buildings to take the brunt of the force. Exposure C structures may be in open fields, with little help protecting them from wind. Exposure D is the most intensive and includes mostly structures located on the water, with nothing to protect them from the full impact of the wind.
Since this project was in an Exposure D category, it would require specific testing and engineering to clear local codes and ensure it can withstand some of the harshest weather Florida has to offer.
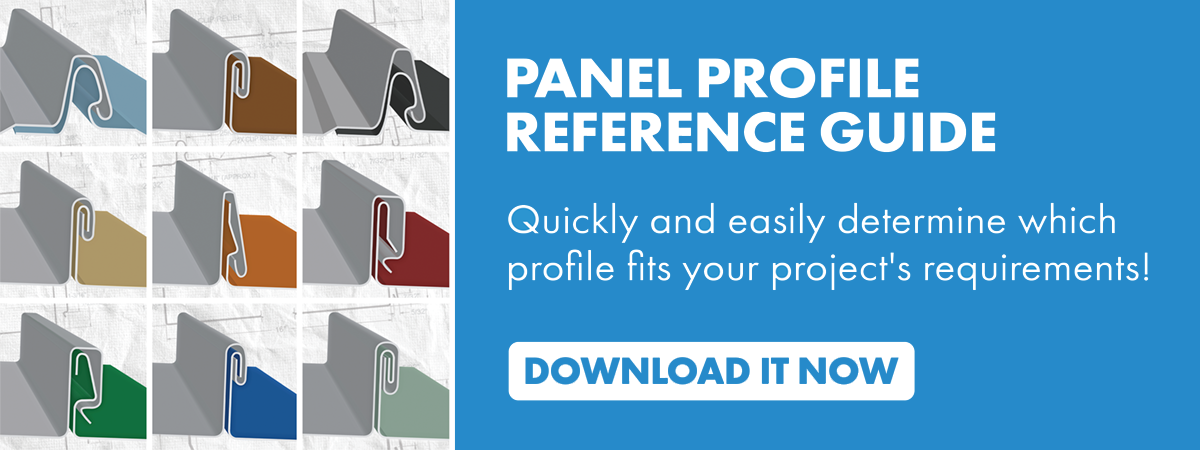
How Integrity Metals Succeeded
One of the most significant drivers of success in this project was choosing the right materials and roofing system. Finding the right match of functionality and aesthetics would fulfill the vision of the radius roof design while defending the roof from premature failure.
Here’s the products and materials they used to achieve their goals:
1.5” Mechanical Standing Seam Panel
“With the arch on the roof having six radiuses, you really can’t do this with an exposed fastener system. You have to use something with a standing rib to put the necessary pressure on it to go around the radius. Standing seam is a must in this case. We had three options: 1″ mechanical, 1.5” mechanical, or 2” mechanical. The 1” felt too small with the 14” fascia, and the 2” was too industrial. So, we settled on the 1.5” mechanical.”
-Joe Keene, Integrity Metals
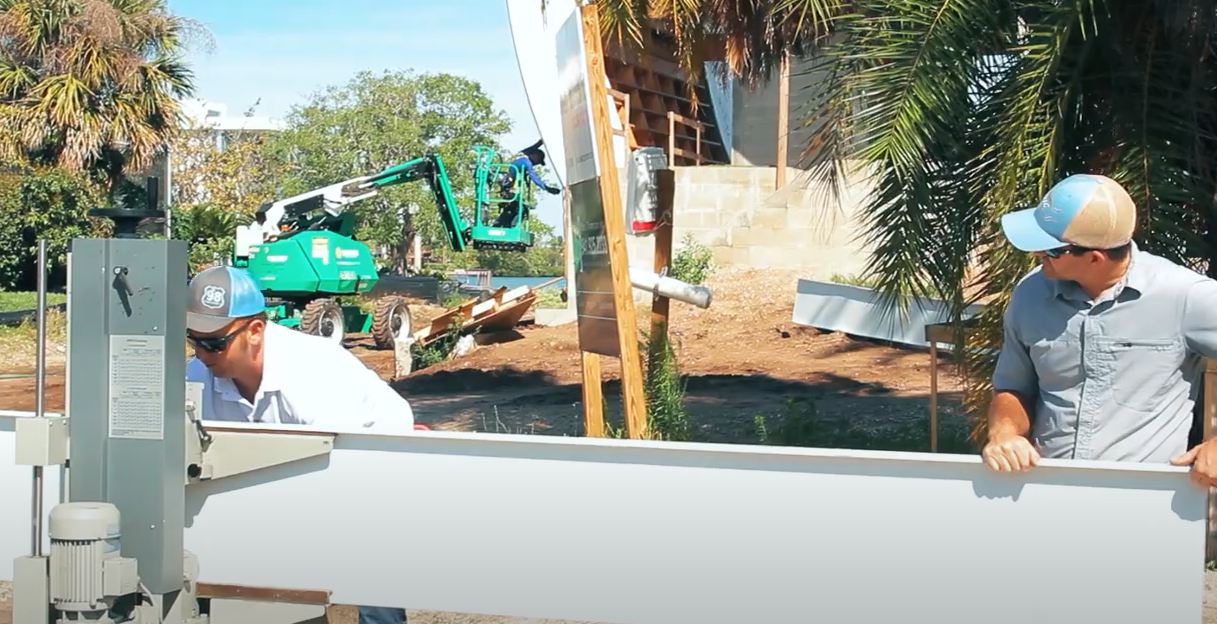
A standing seam metal roof was the clear choice for this project. Integrity Metals needed a standing rib to apply the necessary pressure for it to stretch around the radius of the roof. Plus, standing seam systems often come with various engineered options that already have wind uplift testing, making it the perfect option for the wind-heavy location.
They settled on the 1.5” mechanical standing seam metal roof panel.
The sleekness of the standing seam panels would maintain the modern look of the roof while keeping it protected from the Florida elements.
0.032 Aluminum
“As we’re backing up to brackish water and within a Frisbee toss of full saltwater with breaking surf, [aluminum] is very important.”
–Joe Keene, Integrity Metals
Integrity Metals utilized 0.032 aluminum for this project. Aluminum was the ideal material selection because it has the best defense against saltwater corrosion. Instead of rusting as steel does, aluminum oxidizes as it begins to rust, protecting it from the typical adverse effects of corrosion and retaining its smooth appearance.
Aluminum is also easier to work with because it’s more malleable than steel. Plus, Sheffield Metals offers a coastal warranty on aluminum.
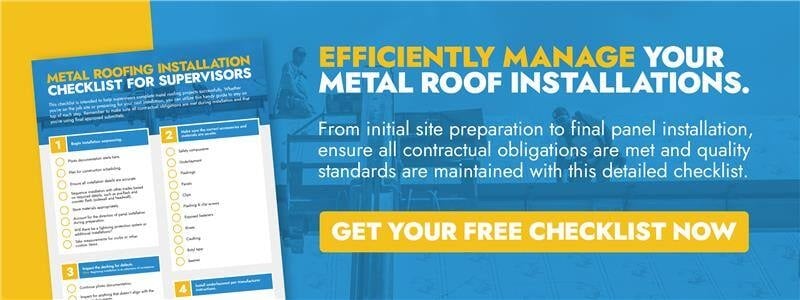
Regal White PVDF Paint Finish
The radius roof project would feature a Regal White PVDF paint finish. Using a PVDF paint finish was crucial because it is the premium paint option that offers improved color retention, great defense against chalking and fading, and exceptional durability. With such a specialty project and its location so near saltwater, this premium finish was needed to ensure a hardy front line of defense for the roof.
Regal White is also one of the most effective colors when it comes to energy efficiency. It’s able to take full advantage of cool metal roofing properties and reflect sunlight, which can be very beneficial in a hot climate like Florida.
On-Site Portable Rollformer
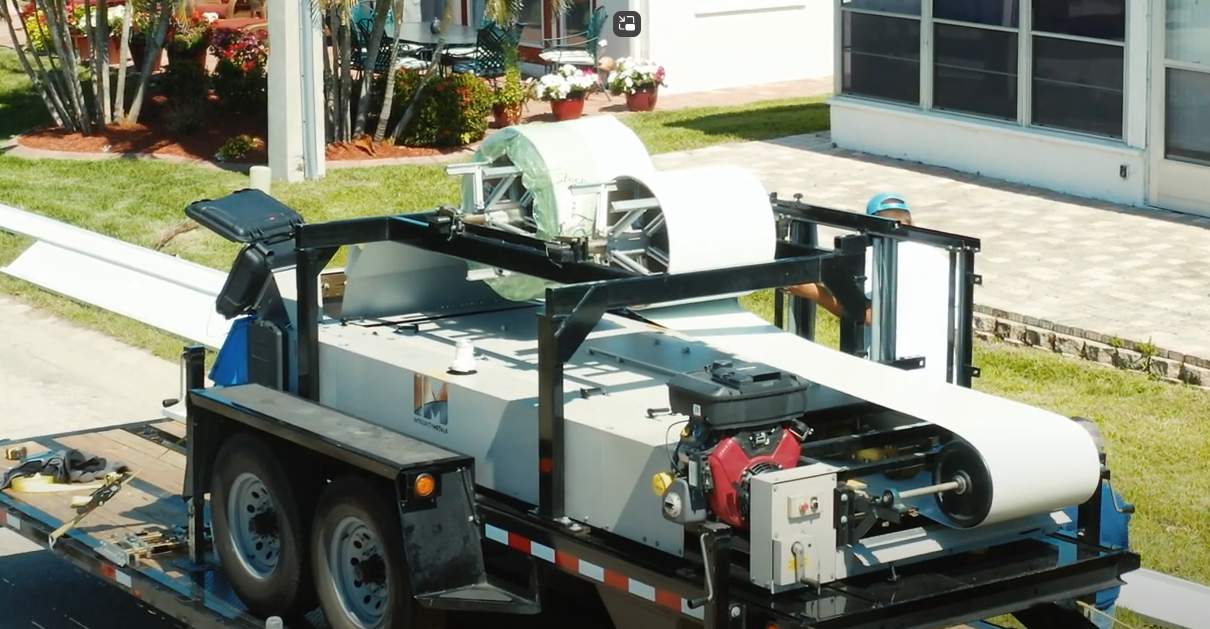
“For this project, portable rollforming is a perfect solution. We can make changes as we need to, and it allowed us a lot of flexibility in what we do. It really makes a difference for a job like this.”
-Joe Keene, Integrity Metals
A key driver of success for this project was the on-site portable rollformer: New Tech Machinery’s SSQ.
The SSQ allowed Integrity Metals to conveniently roll panels on the jobsite. The machine also provided the team with the ability to adjust to specific measurements if needed and make changes on the spot to fit the design.
Portable Radius Machine
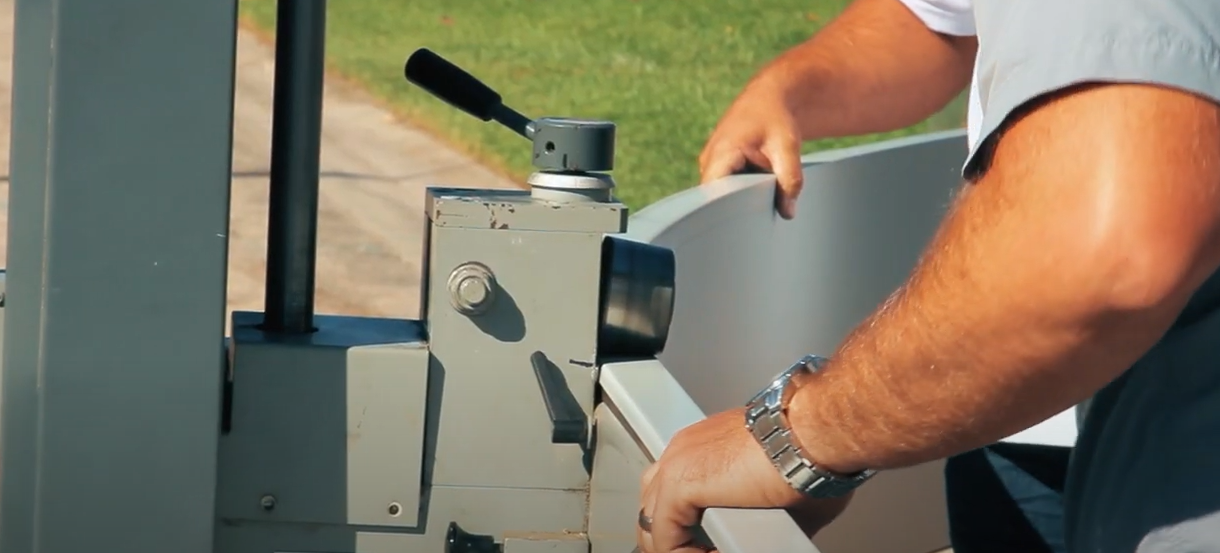
“The uniqueness lies in the barrel roof with six different radiuses, ranging from 212’ to 8’. Some radiuses complete a circle out of a 16’ panel, while others take 424’. Mathematically, being able to know exactly when the points intersected and when radiuses change was a challenge. We had to ensure the trims fell out appropriately, given that the plywood layer added an inch and changed the dimensions. We were 200 miles away from the site, so getting it right was crucial.”
-Joe Keene, Integrity Metals
To achieve the curvature of the roof, Integrity Metals operated a portable radius machine that applied pressure into the male and female rib of the panel. Supporting the sides of the legs and applying pressure allowed them to achieve the radius. The machine needed to be altered at various points throughout the project to maintain the right curvature of the roof.
Installation and Specialty Details
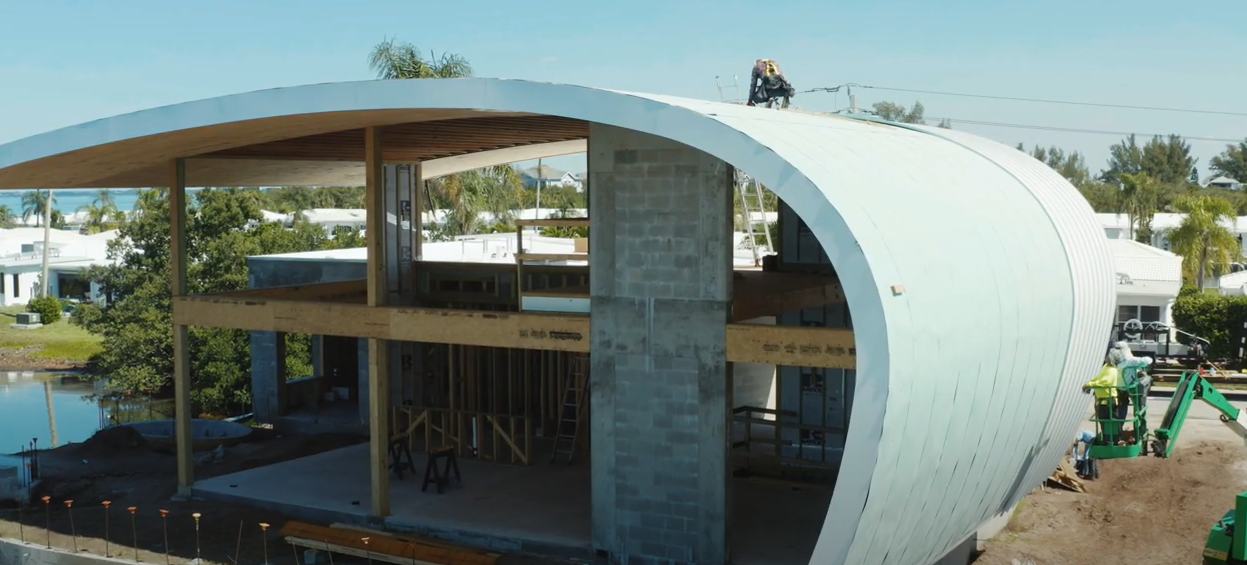
As this wasn’t a typical roof slope, the radius design required unique engineering solutions:
- Custom Trim: Integrity Metals hand-cut a two-piece gable trim to match the radius of the roof. They used hand rollers to make the kickouts and hems, and Pittsburgh-seamed the top for a smooth, linear finish.
- Flashing Areas: For flashing, the team ran aluminum coil upside down through the rollformer, using the leg of the standing seam panel as a Z-flashing. This innovative approach reduced the need for manually making trim in a shop, saving time while ensuring a perfect match to the roof’s curves.
Results
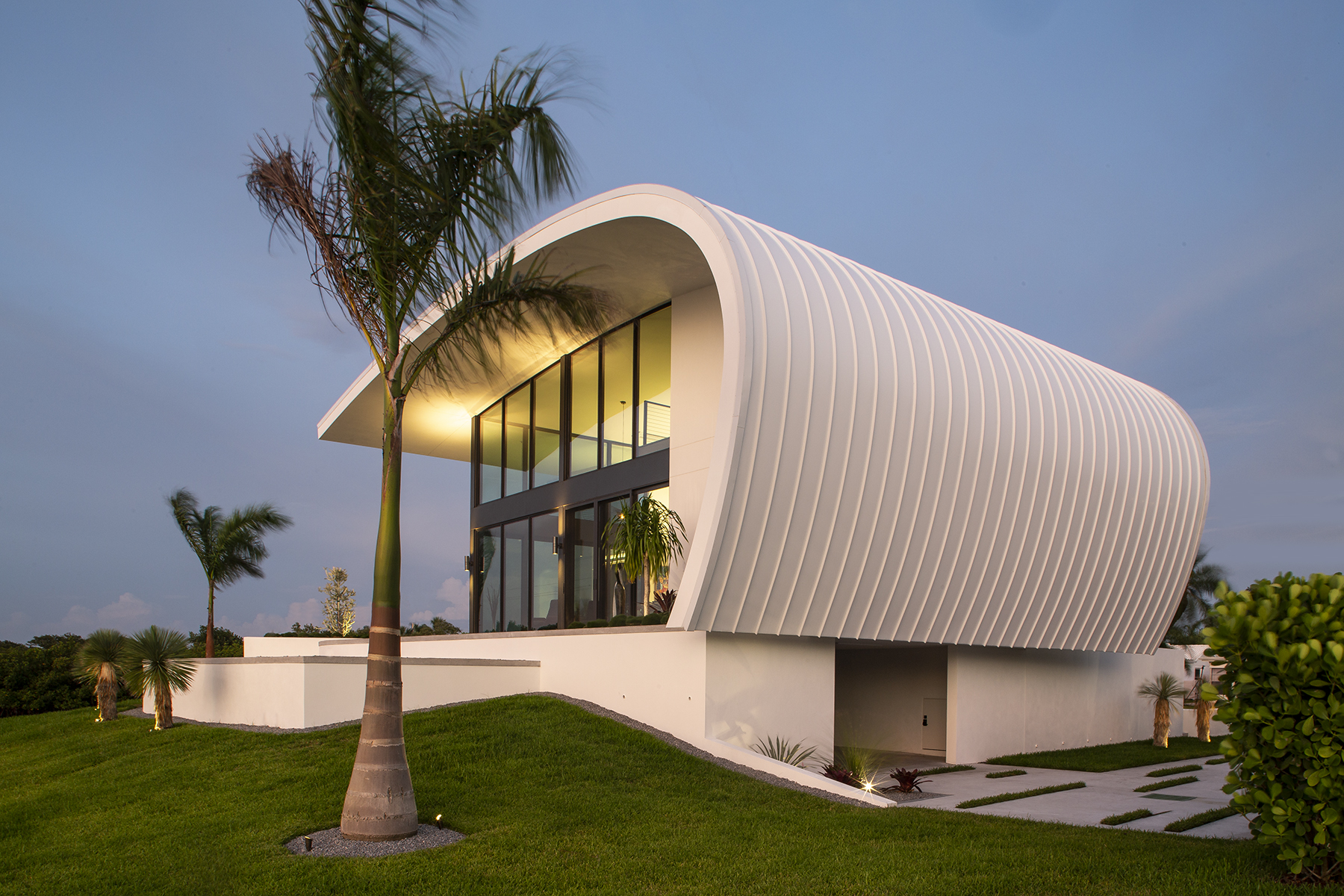
Integrity Metals completed the project with precision, answering the architectural needs of the design and the environmental demands of the Florida coast. By utilizing Sheffield Metals materials — a standing seam metal roofing system with aluminum materials and a PVDF finish — the contractor achieved a visually striking and corrosion-resistant structure that could stand up to Florida’s stringent wind and weather requirements.
Key Takeaways
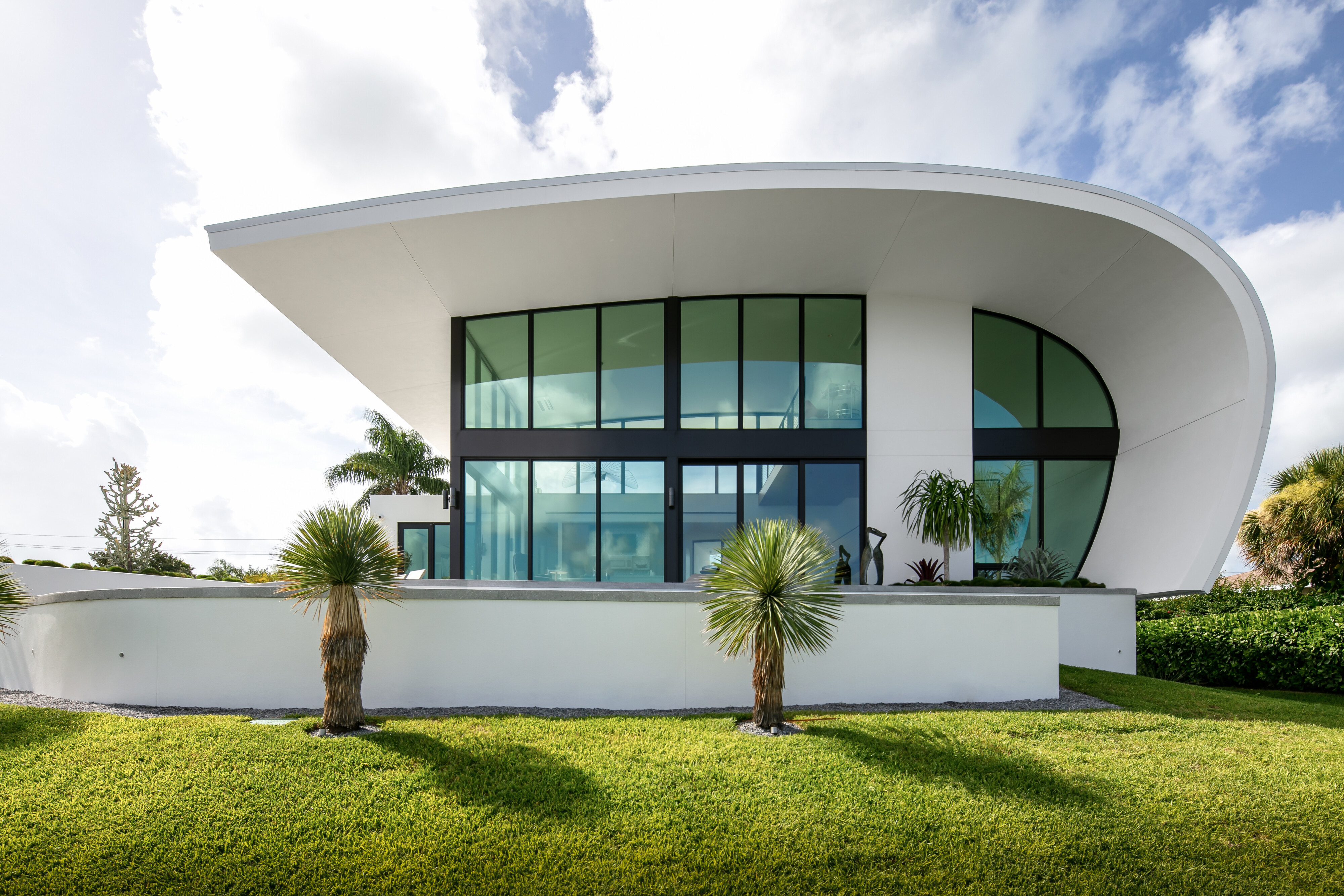
A 1.5” mechanical standing seam metal roofing system met the modern look of the radius roof design and provided the required engineering.
Aluminum roofing materials defended against saltwater corrosion and allowed for easier workability during installation.
A PVDF paint system offered a premium finish as a trusted first line of defense for the metal roof.
New Tech Machinery’s SSQ portable rollforming machine offered convenience and flexibility on the jobsite, enabling Integrity Metal to cut custom measurements efficiently.
Integrity Metal’s experience with specialty projects and metal roofing in general, plus its ability to problem-solve and find solutions on the spot, like the custom trim solutions and flashing areas, led to an impressive result that may not have been possible to achieve with standard methods.
This project highlighted the importance of choosing the right metal roofing materials from a reliable supplier, purchasing the right equipment, and having an in-depth knowledge of both the technical and architectural side of metal roofing.
Need Help with Your Next Metal Roofing Project?
Sheffield Metals is ready to help with your next project, whether that’s a simple picnic area metal roof or a complex, specialty design like the one covered in this article. We have the materials to set you up for success.
Aside from providing coils, sheets, and accessories like clips and fasteners, we are also committed to giving customers support throughout their entire project. We have an architectural team who can provide guidance on metal roof designs. Our commercial team can assist with navigating submittals and gathering the correct documents for a commercial job. And our technical team can provide information on installation details and engineering for various panel profiles.
Reach out today to start a partnership with Sheffield Metals.
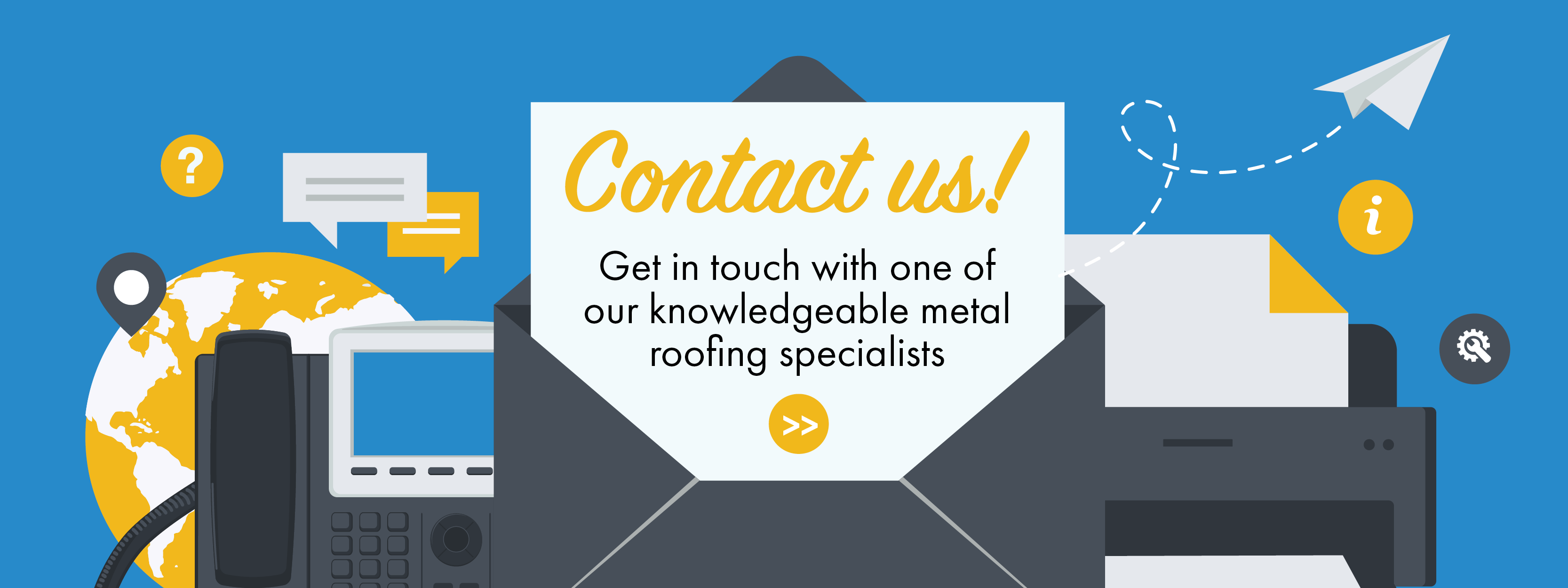