Metal Roof Testing: What Are the Standards for Metal Roof Materials?
Industry standards exist for nearly everything — food, medicine, and yes, metal roofing systems. It's important to know these industry standards so you can provide peace of mind to your...
“How do I know my metal roof won’t puncture during a hailstorm?”
“Will my roof system hold up during a tropical storm with high wind speeds?“
“How can I verify that water won’t leak through the panel seams?“
It’s important to know the ins and outs of what makes a metal roofing system perform to the best of its ability.
The best way to accomplish this is by familiarizing yourself with the common industry standards and tests metal roofing goes through to ensure the success of a system. Once you know these standards, you’ll be able to reassure your customers (or yourself) that the metal roof is tested and proven to perform in harsh weather conditions.
In all honesty: There are a lot of metal roofing standards and they tend to be complex, which might confuse even the most seasoned person in the industry. Our Sheffield Metals Technical Department works with contractors and manufacturers every day regarding this topic, so we know how to simplify this topic and help you to understand:
- The importance of metal roofing industry standards.
- What businesses/companies perform the tests for metal roofing standards.
- How the tests and standards vary depending on location, job type, and various other factors.
- Common standards in metal roofing and how the products are tested.
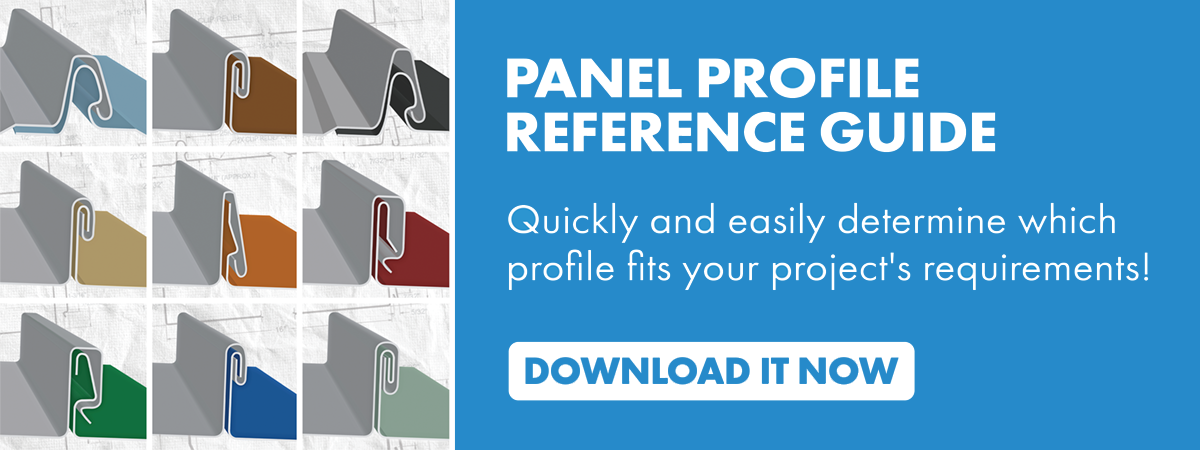
The Importance of Metal Roofing Industry Standards
The reason that standards and testing exist can be summed up with one word: Trust.
Consumers need to trust the products and services they spend their money on and that they will live up to expectations and solve the problem it’s designed to fix. This is why standards exist for nearly everything; food, medicine, paper products, electrical wires, and far beyond.
So why does it matter for metal roofing? Standards and testing ensure that a metal roofing system can protect a building or home in both regular and extreme weather conditions while still meeting the building and construction codes of the industry and local municipalities.
Standards help:
- Provide peace of mind to suppliers, contractors, architects, and consumers by proving products will perform — instead of saying, “Just take our word for it.”
- Remember, many consumers buy metal roofing because it protects their most valuable assets, such as loved ones, investments, photos, files, etc.
- Stop untrustworthy manufacturers from selling low-quality products that could fail or cause problems.
- Put accountability for product quality in the hands of the manufacturer.
Who Does the Testing For Metal Roofing Standards?
The good news is that metal roofing is tested and rated by independent businesses and organizations with no stake in one specific industry, which allows for a more trustworthy and honest analysis. The company provides the standards and specifications for products and materials far beyond roofing. In other words, they create the testing protocol that best measures product performance in real-world scenarios.
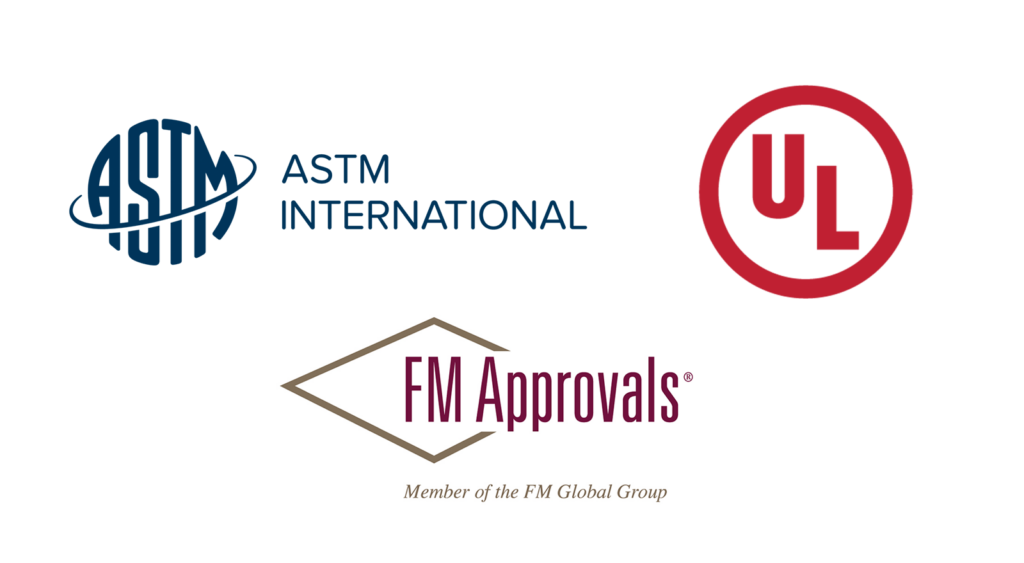
However, as it applies to metal roofing, three companies provide the majority of testing standards:
While these companies outline the parameters of how products will be rated based on their performance, they don’t perform the testing. Instead, a third-party testing facility performs the test. Usually, a representative from one of these standards companies is present to report the findings and provide the final results and/or ratings.
Like the test standard companies, the testing facilities just perform the tests and provide the results. Their primary concern is that they perform the test accurately according to the test standard and not how the product performs.
Industry Standards & Testing for Engineered Metal Roofing Systems
Before we go through some common industry standards for metal roofing systems, it’s important to know that these standards and tests can and will differ depending on geography and building type. It’s impossible to account for every standard because one or more will either be missing or not applicable in a given geographic location.
For example, a building or property in a hurricane zone in Florida will require different test standards than a building in rural Kentucky, which is why multiple test standards may sound similar but are very different. Wind uplift resistance can be tested according to UL 580, UL 1897, TAS 125, and ASTM E1592 standards, just to name a few. All of them test for wind uplift resistance, but some tests are more stringent, require multiple specimen examples to be tested, are dependent on the type of structure it’s installed on, or test to higher standards than others do. This is the same for impact resistance, water penetration, and more.
Additionally, commercial and residential metal roofing differ in standard requirements — even with structures in the same geographic location. Commercial projects have more stringent requirements and must meet the standards set forth by the industry. But residential projects are a little different, as they are more focused on adhering to local building codes and having the correct permits, which are available and able to be pulled by a municipality’s Building Department. It’s worth noting that all roofs have minimum requirements per municipality or Building Department, and even some architects may require different standards that specified products must meet. For example, sometimes ASCE 7 is specified and requires an engineer to validate uplift requirements and load exerted on a roof.
In other words, the required tests and standards simply depend on the project.
If you’re unsure about the required standards for your metal roofing project, strike up a conversation with your manufacturer or supplier. They can answer your questions and provide a more comprehensive scope of the ratings, standards, or tests a product should adhere to, and why it should or shouldn’t be used for your metal roofing project.
UL 580 / UL 1897 – Standard for Tests for Uplift Resistance of Roof Assemblies
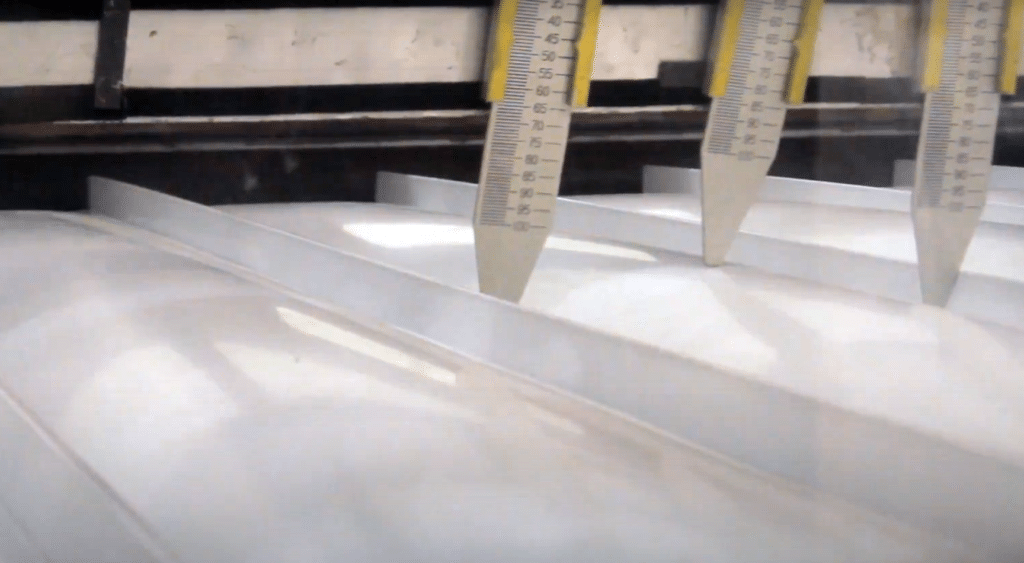
The UL 580 standard tests the uplift wind resistance of a metal roofing system, including the panels, accessories (clips, underlayment, and fasteners), and structural support frame.
A small-scale (typically 10×10 ft.) sample of roofing material is installed on the testing platform. The edges are then sealed with closely spaced fasteners. This test is a pass or fail, and is completed in three UL 580 sequences, and then turns into a UL 1897 if it can go beyond Class 90 (and tests until the system fails):
- UL 580 Class 30
- UL 580 Class 60
- UL 580 Class 90 (best)
- UL 1897 test
- Maintains a positive pressure and increases in negative pressure usually in increments of 15 PSF until the system fails.
- Note: This is the same system being tested throughout all sequences, so new specimens are not used as the test progresses.
Each of these sequences consists of five phases:
- Phase 1: 5 minutes of negative pressure (measured in pounds per square feet, or PSF)
- Phase 2: 5 minutes of negative and positive pressure
- Phase 3: 60 minutes of cyclic (oscillating) negative and positive pressure
- Phase 4: 5 minutes of negative pressure
- Phase 5: 5 minutes of negative and positive pressure
For an example of the pass or fail results, check out the UL 580 test report for SMI’s 1.5” SnapLock 550.
ASTM E1680 – Standard Test Method for Rate of Air Leakage Through Exterior Metal Roof Panel Systems
According to the ASTM E1680 standard:
This test method covers the determination of the resistance of exterior metal roof panel systems to air infiltration resulting from either positive or negative air pressure differences … This test method is intended to measure only the air leakage associated with the field of the roof, including the panel side laps and structural connections; it does not include leakage at the openings or perimeter or any other details.
Like UL 580, ASTM E1680 tests using a small-scale roofing system, including panels, clips/cleats, and a support frame.
The test consists of six separate preload pressures (three complete cycles of preload pressures) all at a specific pressure (in PSF), followed by measurement of the air infiltration and air exfiltration through the panel, which is measured in cubic feet per minute (CFM).
- Positive preload
- Negative preload
- Positive preload
- Negative preload
- Positive preload
- Negative preload
- Air infiltration measurement
- Air exfiltration measurement
Based on the measurement collected in the final two steps, you can determine the rate at which air is expected to leak through properly installed panels.
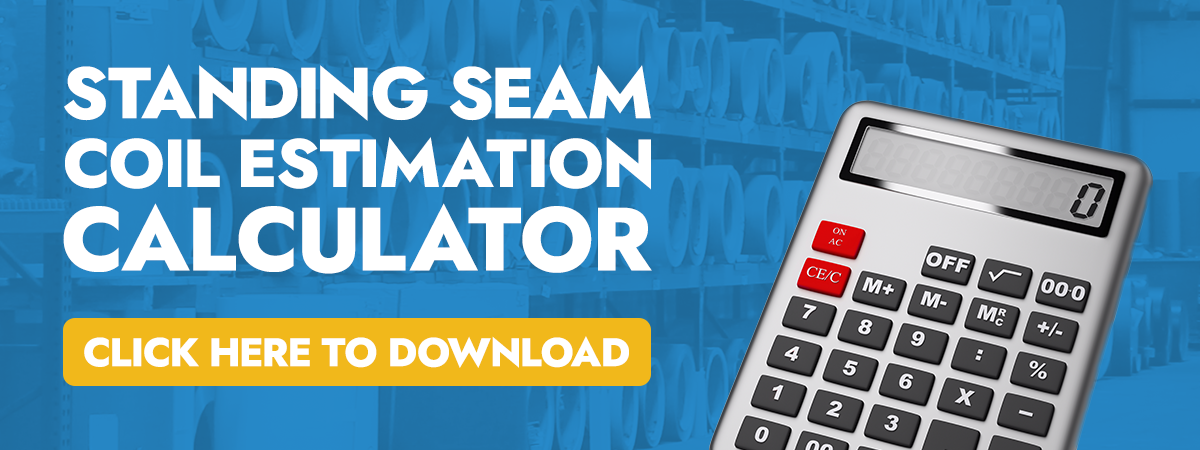
ASTM E1646 – Standard Test Method for Water Penetration of Exterior Metal Roof Panel Systems by Uniform Static Air Pressure Difference
The standard for water penetration, ASTM E1646, is similar to the air infiltration test. This is another pass-or-fail test.
According to the scope of the standards:
This test method covers the determination of the resistance of exterior metal roof panel systems to water penetration when water is applied to the outdoor face simultaneously with a static air pressure at the outdoor face higher than the pressure at the indoor face, that is, positive pressure … This test method is applicable to any roof area and is intended to measure only the water penetration associated with the field of roof including panel side laps and structural connections. It does not include leakage at openings or perimeter or any other details.
After the pre-determined air pressure is reached, water is sprayed on the panels for a duration of 15 minutes. The amount of ponded water is determined and then the amount of water infiltration through the tested panel is measured.
ASTM E2140 – Standard Test Method for Water Penetration of Metal Roof Panel Systems by Static Water Pressure Head
ASTM E2140 is a water penetration test evaluating the resistance of roof panels, sideseams, endlaps, and roof plane penetrations to water submersion.
According to the standard’s scope:
This laboratory test method covers the determination of the resistance to water penetration of exterior metal roof panel system sideseams, endlaps, and roof plane penetrations when a specified static water pressure head is applied to the outside face of the roof panel.
During this test, the roof panel system is completely submerged under water to test its ability as a water barrier. This test method is intended to evaluate water-barrier (not water-shedding) roof system joints and details. These systems are also referred to as hydrostatic roof systems (roofs with a slope below 2/12).
UL 2218 – Standard for Impact Resistance of Prepared Roof Covering Materials
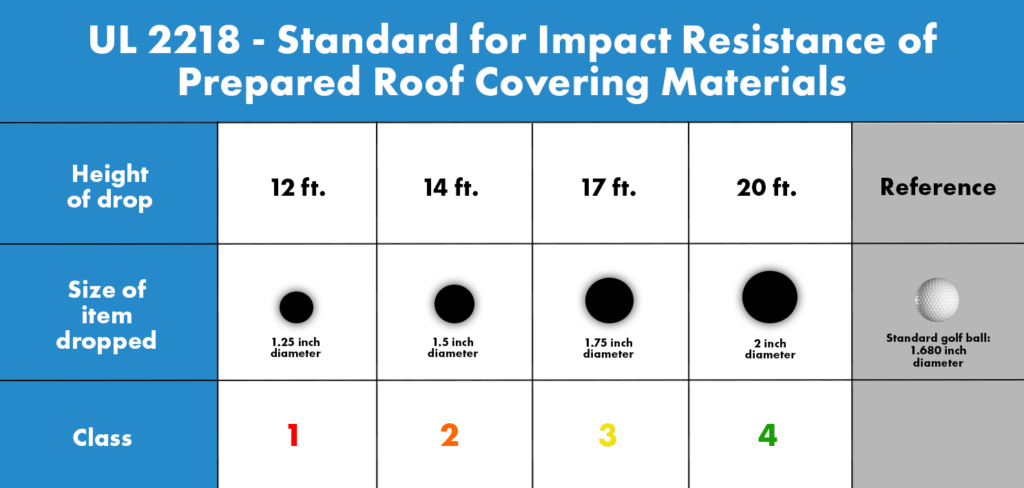
The industry guideline UL 2218 tests a metal panel’s resistance to puncturing or failing when it comes into contact with items, such as hail or other small debris.
The testing method “…provides impact resistance data for the evaluation of prepared roof covering materials…The test evaluates the effect of impact from a steel ball at locations on the assembly selected to be most vulnerable, such as (but not limited to) edges, corners, unsupported sections, and joints.”
Four steel balls of different sizes are dropped from varying heights onto the metal panels (see the above photo for parameters). The panels are then evaluated to see if punctures or other failures have occurred.
Rating is determined on a scale from Class 1 to 4, with Class 4 being the toughest and least likely to fail when in contact with objects.
UL 790 – Standard Test Methods for Fire Tests of Roof Coverings
One of the most important tests on a metal roofing system is its resistance to combustion and/or catching on fire.
According to UL’s Standard Catalog:
These requirements cover the measurement of the relative fire characteristics of roof coverings exposed to simulated fire sources originating from outside a building on which the coverings are installed. They are applicable to roof coverings intended for installation on either combustible or noncombustible roof decks when the roof coverings are applied as intended.
After testing, roof materials are given one of three fire ratings:
- Class A – “Roof coverings are effective against severe fire test exposures. Under such exposures, roof coverings of this class afford a high degree of fire protection to the roof deck, do not slip from position, and are not expected to produce flying brands.”
- Class B – “Roof coverings are effective against moderate fire test exposures. Under such exposures, roof coverings of this class afford a moderate degree of fire protection to the roof deck, do not slip from position, and are not expected to produce flying brands.”
- Class C – “Roof coverings are effective against light fire test exposures. Under such exposures, roof coverings of this class afford a light degree of fire protection to the roof deck, do not slip from position, and are not expected to produce flying brands.”
Most metal roofing and wall systems are Class A fire-rated and noncombustible, making them the most resistant to combustion and catching on fire.
Industry Standards & Testing for Paint Specifications
Metal roofing paint systems come with standards and testing that ensure the success of a paint system. We won’t dive too deep into these standards, but just know that there are various. However, adhering to them is the responsibility of the paint company, such as Sherwin-Williams, to test before the paint ever reaches a metal coil.
Metal roofing paint systems endure stringent testing, like the natural outdoor exposure test in the photo, to ensure the paint system stands up to chalking, fading, chipping, peeling, and other overall failures.
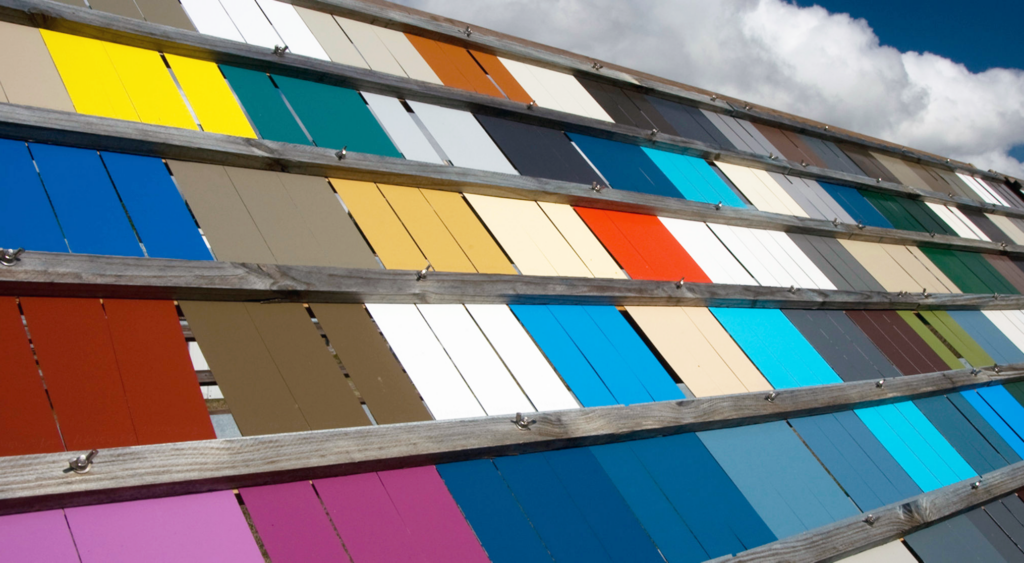
For example, a standard two-coat polyvinylidene fluoride (PVDF) typically adheres to the following standards set forth by ASTM:
- Accelerated weathering – ASTM G23
- Salt spray – ASTM B117
- Humidity – ASTM D2247
- Formability – ASTM D3359
- Pencil hardness – ASTM D3363
- Impact resistance – ASTM D2794
- Specular gloss – ASTM D523
- Acid resistance – ASTM D Procedure 72
- Abrasion resistance – ASTM D968
- Tunnel test – ASTM E84
In other words, the paint goes through a lot of testing to make sure it doesn’t crack, chalk, fade, peel, or succumb to any other damage prematurely. These tests are why many paint manufacturers guarantee their PVDF products with lengthy metal roofing and wall system paint warranties. If you have questions about the testing that goes into a panel’s given paint system, we recommend contacting the paint manufacturer.
Final Thoughts on Metal Roof Testing & Standards
Remember, there are many other standards, tests, codes, and regional requirements that apply to metal roofing and wall systems. However, the ones we outlined are a good representation of common standards and testing currently in the roofing industry.
At Sheffield Metals, we know how important it is to maintain customer trust, part of which comes from being able to talk through and explain how their metal roof will perform in certain situations.
Get ahead of these questions and contact us today to speak with one of our technical representatives.
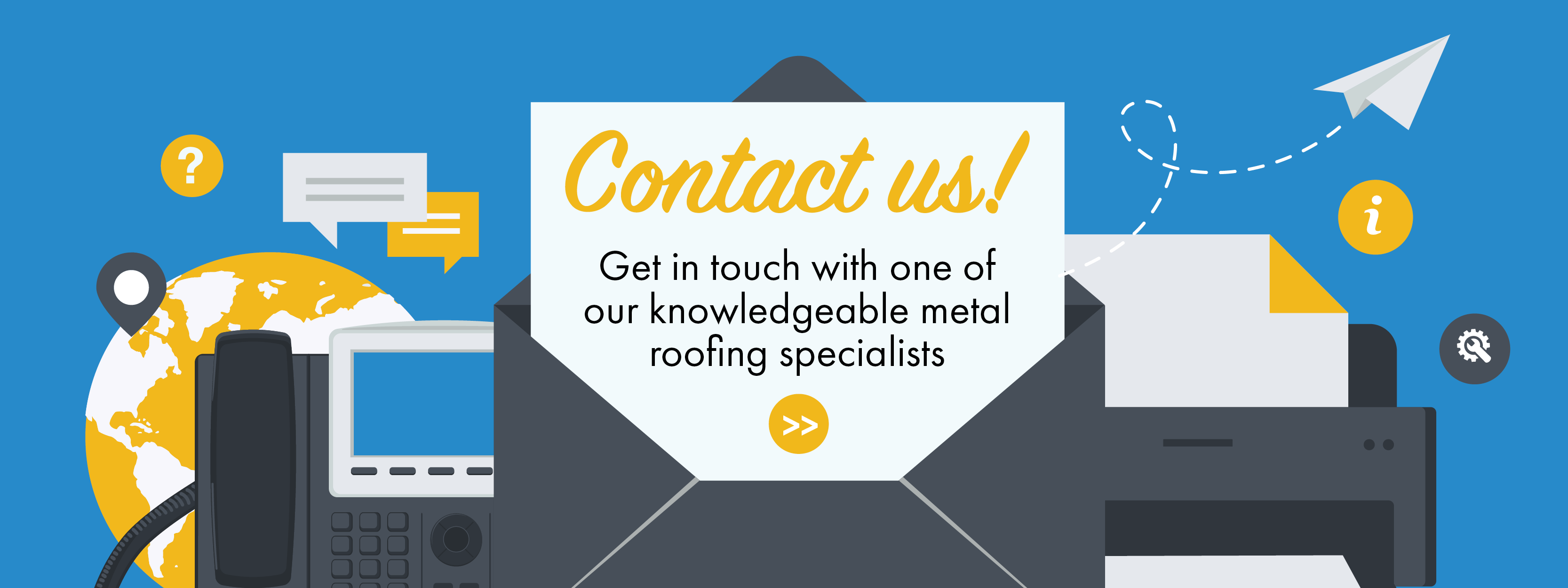