What is ZAM®? Advantages and Best Applications of the Wheeling-Nippon Substrate
Get a complete overview of ZAM®, its unique benefits compared to galvanized and Galvalume®, and where it performs best in real-world applications.
If you’re a contractor in the metal roofing industry, you know how important it is to understand the details of every product that goes into the full assembly. What’s underneath the paint is just as important as the topcoat.
And a lesser-known substrate like ZAM® can immediately raise red flags — what is it, why is it being used, and how does it stack up against traditional substrates like Galvalume®?
In this article, we’ll answer all those questions. By the time you’re done reading, you’ll have a better understanding of what ZAM is and why it’s worth your attention.
What Is ZAM?
ZAM is a hot dip coated steel made with Zinc, Aluminum, and Magnesium, produced by Wheeling-Nippon Steel. Basically, it’s a steel sheet with a unique metallic coating that provides exceptional corrosion resistance.
The alloy combines various advantages into one — the barrier protection of aluminum, the self-healing properties of magnesium, and the durability and hardness of zinc. It’s produced to ASTM A1046/A1046M Type 1 specifications.
ZAM is sometimes considered to be a “bridge” between galvanized steel and stainless steel, as it offers exceptional corrosion resistance at a reasonable price.
ZAM Specifications
- Material Thickness: 0.014”-0.130”
- Material Width: 24”-61”
- ASTM Specification: ASTM A1046/A1046M Type 1
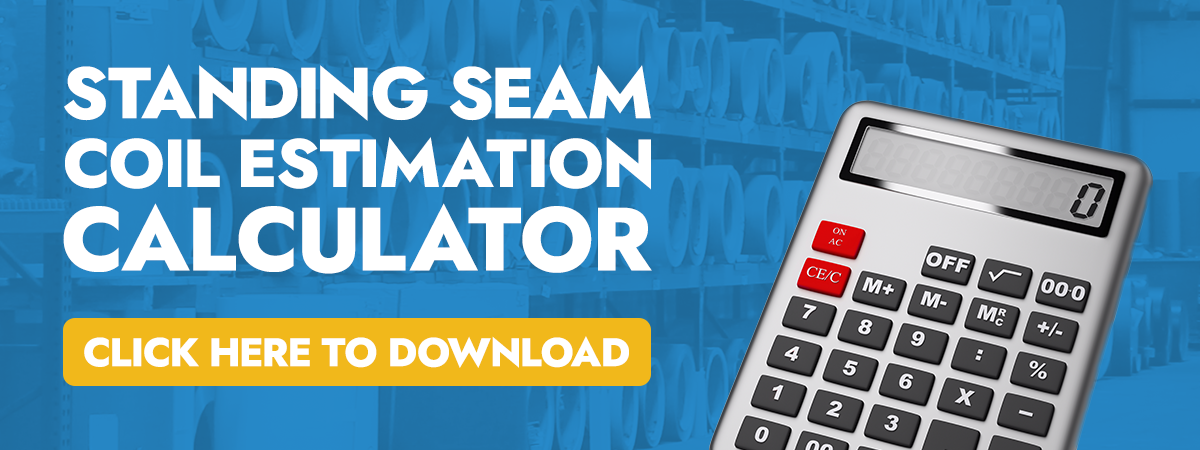
What are the Advantages of ZAM?
Corrosion Resistance
When ZAM is exposed to moisture and begins to corrode, it produces thin, zinc-based oxide/hydroxide films enriched with aluminum and magnesium that are highly stable and protective.
Side-by-side salts spray tests show ZAM withstanding red rust much longer compared to traditional coatings. ZAM has also outperformed galvanized coatings in corrosion resistance by 10 to 20 times. Over the course of 14,000 hours in a salt spray test, ZAM showed little signs of rust, while the Galvanized steel had clear, visible signs of corrosion.
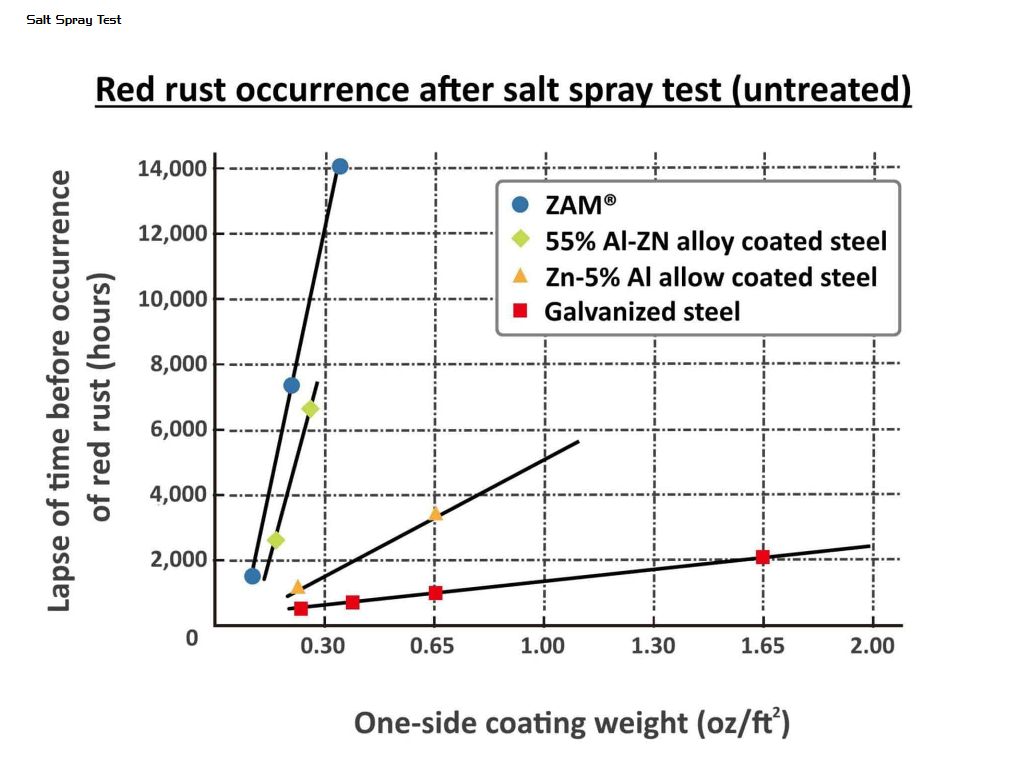
ZAM® is a coined name applied to the hot-dipped zinc-aluminum-magnesium-alloy-coated steel sheets developed by NIPPON STEEL CORPORATION
® WHEELING-NIPPON STEEL 2024
Note that some warranties for ZAM still will not cover projects within 300 feet of the ocean coastline with breaking surf or in areas of constant salt spray. Also, warranty coverage will differ based on coatings weights. It’s essential to read your warranty to understand the fine points — refer to your specific warranty documentation to get the specifics of what will cover your project.
Self-Healing Abilities
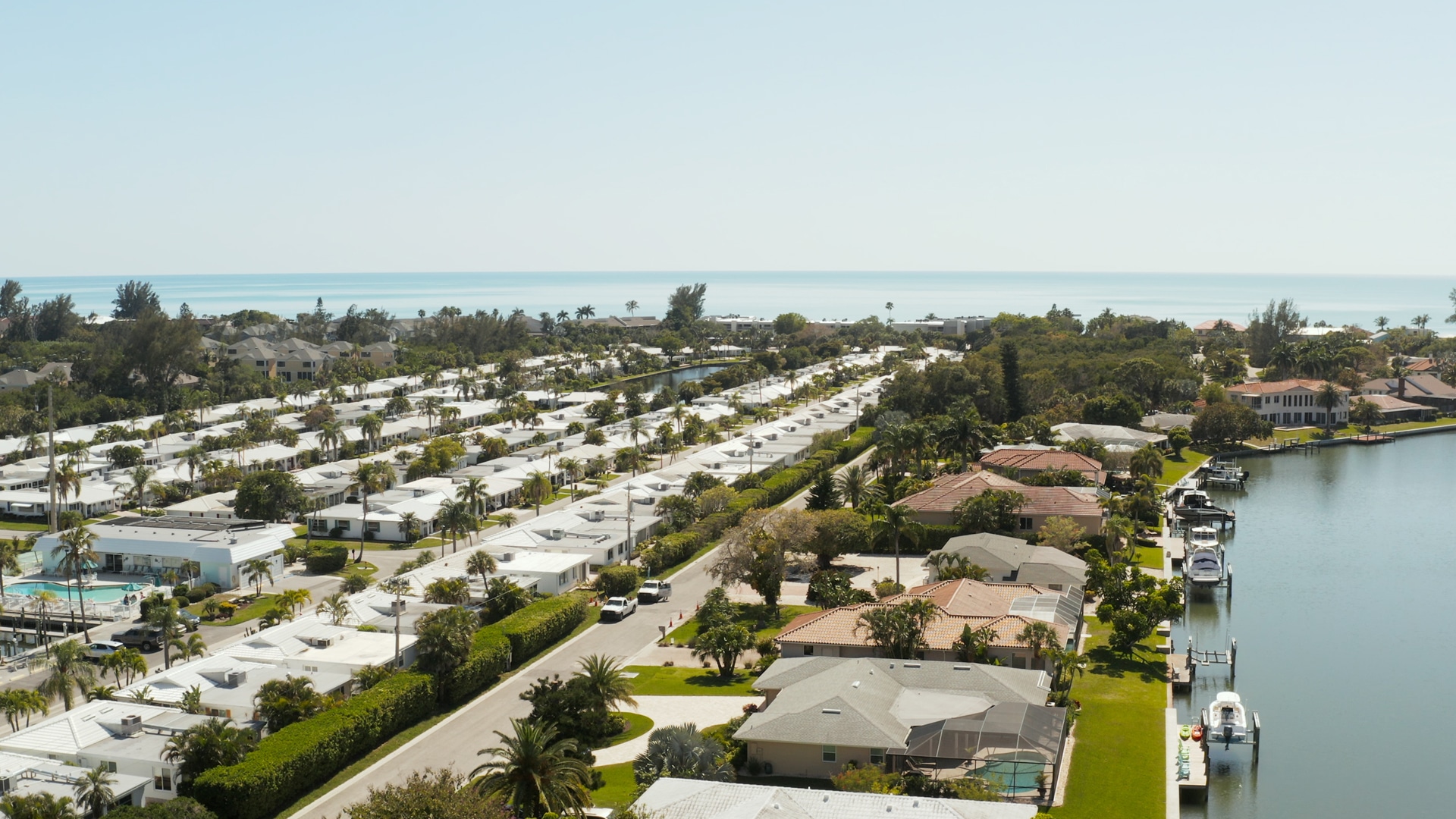
Any time you cut, drill, or scratch a metal panel, that bare steel is exposed to moisture. On traditional substrates, that could leave the metal vulnerable to corrosion sooner rather than later.
ZAM’s magnesium-enriched coating forms a corrosion layer that actually migrates over the exposed steel and locks it down, protecting it from rust. Cut edges, panel ends, and fastener holes will stay protected much longer with ZAM than with other types of substrates.
In a salt spray test on cut edge sections, ZAM again showed little signs of rust after 5,000 hours, while Galvanized steel showed evident signs of red rust within 1,000 hours.
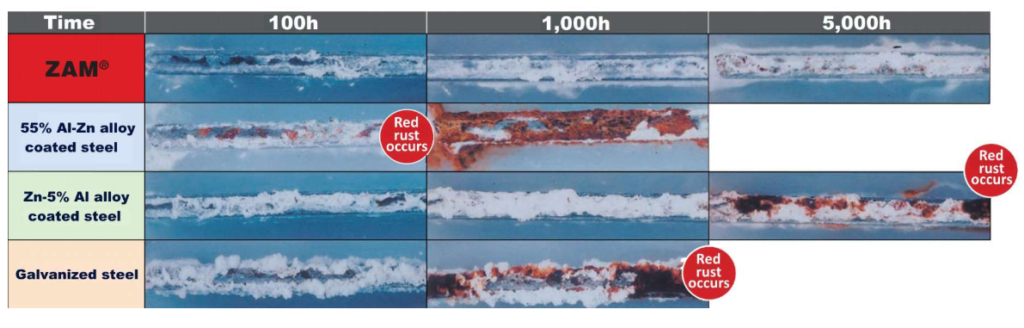
ZAM® is a coined name applied to the hot-dipped zinc-aluminum-magnesium-alloy-coated steel sheets developed by NIPPON STEEL CORPORATION
® WHEELING-NIPPON STEEL 2024
Versatility
ZAM is built for harsh conditions. Regions where traditional substrates struggle — coastal, industrial, or agricultural environments — ZAM can excel, using its self-healing abilities to protect the material and last far into the future.
It’s great for residential homes along the coast and commercial businesses looking to get the most out of their materials. It’s also effective for industrial applications, as the unique alloy of ZAM allows it to protect its materials even in the presence of some corrosive chemicals like ammonia.
Workability
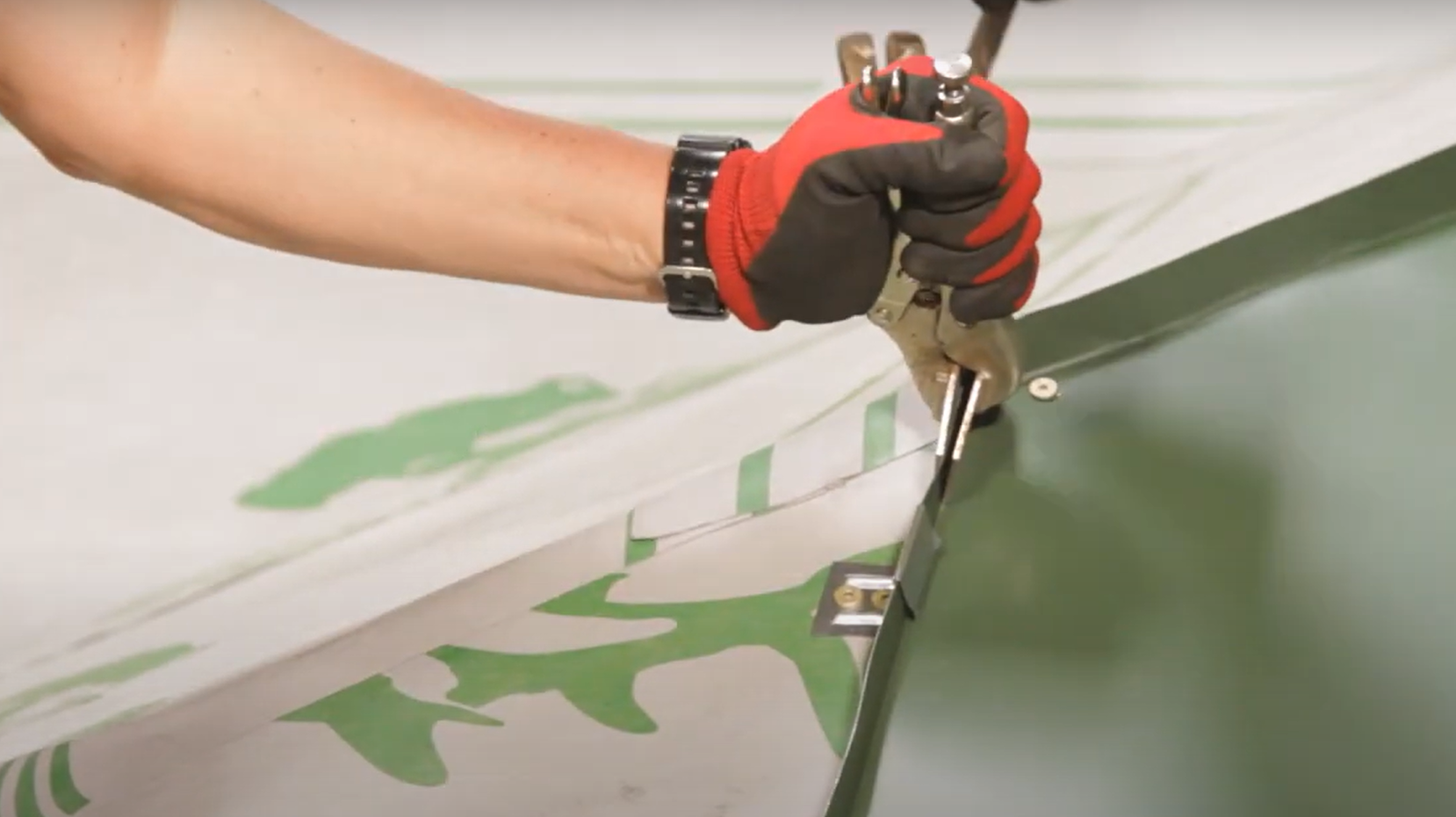
It bends, cuts and rollforms just like galvanized steel. You won’t need new tools or special processes to use ZAM.
Remember the workability of the metal will in part depend on how thick the metal is — thicker metals like 22-gauge will require more labor to bend and cut, while thinner metals — 24 and 26-gauge — will be less labor-intensive.
Eco-Friendly
ZAM is made from 30-60% recycled materials and is 100% recyclable at the end of its service life. Uniquely, ZAM also requires less coating for the desired corrosion resistance. ZAM requires less zinc for its coating and in turn less mining from the earth.
Using less zinc also means that there will be less zinc runoff in the environment. Many cities test for zinc runoff in storm drains.
And lastly, the impressive durability of ZAM means less repairs and replacements in the future, cutting down on material and labor needed and promoting sustainability.
ZAM for Metal Roofing Applications
Residential
ZAM is specially designed to withstand the corrosive effects of salt spray. Homeowners on the coast can rest easy with the zinc-aluminum-magnesium protectiveness of this substrate. Panels will be protected from rust for many years and the roof will require minimal maintenance to keep it looking great.
Especially when it comes to standing seam metal roofing, protecting the entire assembly is crucial to make sure it’s worth the investment and will perform as it should — for decades.
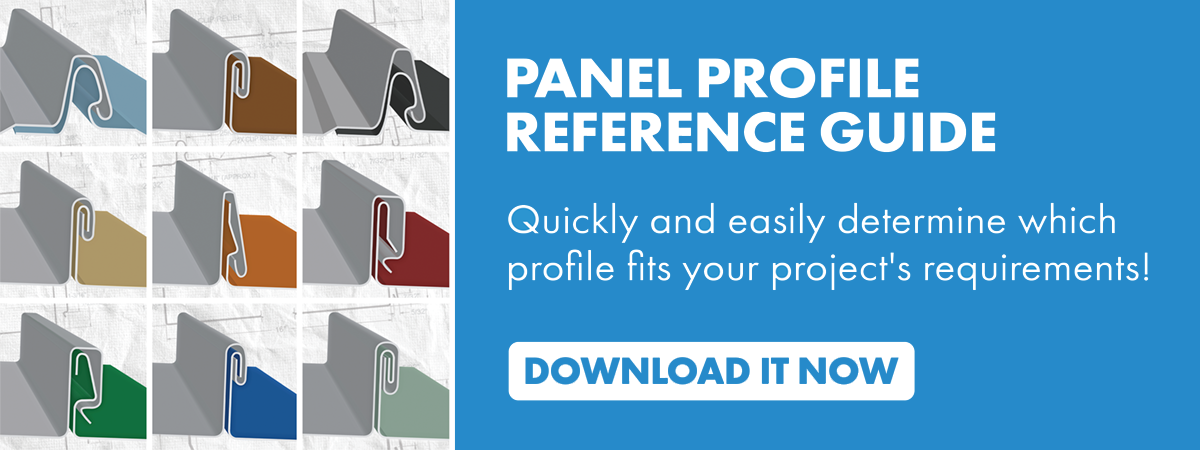
Commercial
For warehouses, office buildings, and retail centers, using ZAM means fewer repairs, longer warranties, and better long-term value for building owners.
Business owners often balance the up-front costs of products against their overall lifespan and maintenance costs. The durability and longevity of ZAM can reduce maintenance disruptions and save money in the long run by cutting down on repairs or replacements. Fewer repainting jobs may be needed, along with fewer repairs at unit mounts or lap joints.
In urban environments, ZAM could be better suited to resist the corroding effects of acid rain or smog. And its versatility makes it an attractive choice for architects looking to have a streamlined, modern look for their design.
Agricultural and Industrial
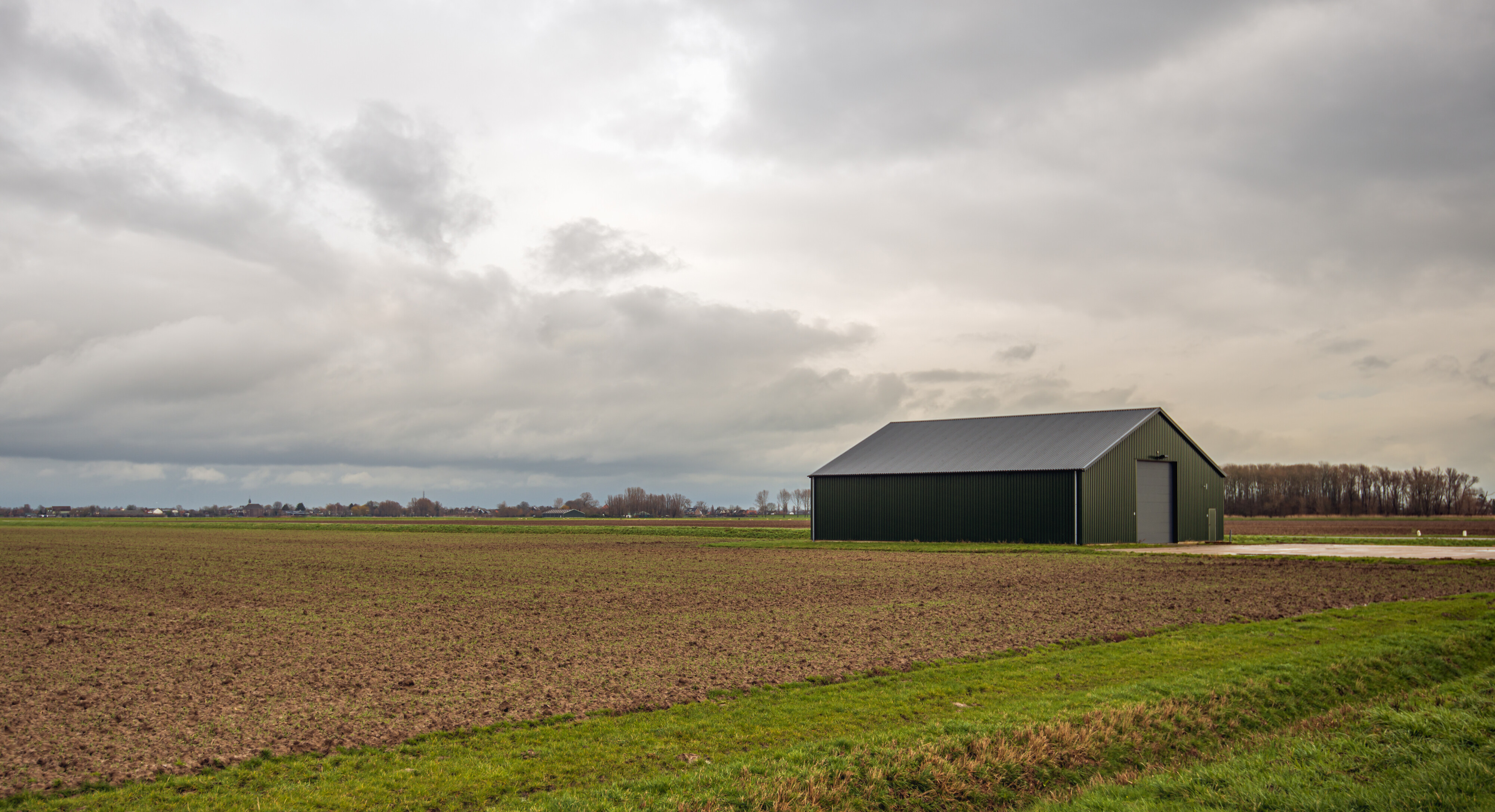
ZAM can hold up well in high-ammonia atmospheres like chicken coops and dairy barns, making it a great cost-effective alternative to stainless steel. ZAM can also be an effective option for solar panel mounting structures, farm equipment and structures, refineries, and fertilizer storage buildings.
How Does ZAM Compare to Other Substrates?
Durability
Metal roofing is one of the best options for homes and buildings due to its durability and longevity. Many materials, including Galvalume and galvanized steel, will provide exceptional performance.
But part of how well your substrate performs will depend on the unique aspects of your project — where your region is located, what the function of your building is (industrial vs residential homes) and the thickness of the material itself. But one definite way substrates differ is their level of corrosion resistance.
Corrosion Resistance
Galvalume is a solid choice for metal roofing applications and has shown time and time again to last for decades without serious problems. However, in coastal applications or aggressive industrial settings, it may start to rust at cut edges or scratches.
Areas near the coast are also typically exposed to wind uplifts, which can be detrimental to some roofing systems. Galvanized steel can offer the strength needed to defend against wind uplifts, while aluminum gives you that corrosion resistance. A happy medium is ZAM — giving you the strength of steel and the corrosion resistance of aluminum at a reasonable price.
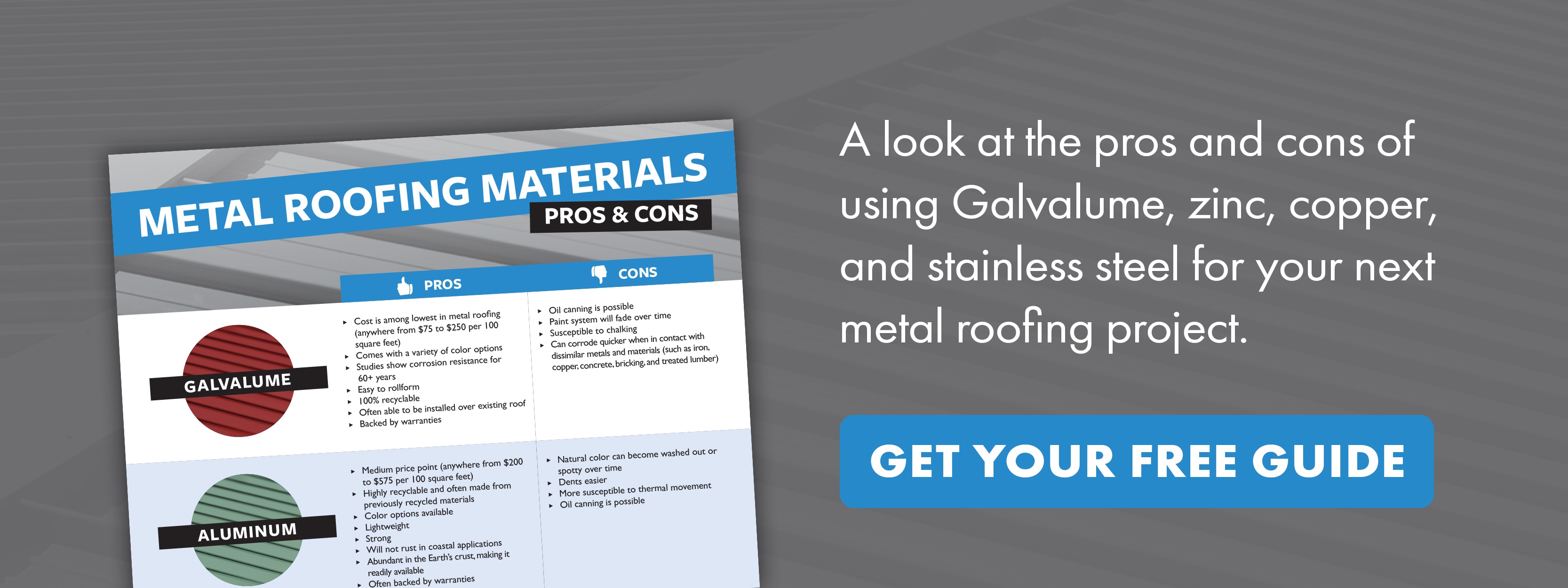
Cost
Galvanized steel has the lowest cost, while Galvalume comes in a bit higher and ZAM is the most expensive per pound. ZAM can be anywhere from 15% to more than 50% more expensive than galvanized steel, but the final price will depend on the product specifications and current market conditions.
Keep in mind, however, that the cost may become closer or even less when the future repairs and replacements are taken into account. Coastal warranties will be available for ZAM substrates and not Galvalume.
ZAM® vs. Galvalume® vs. Galvanized Steel
Feature | ZAM® | Galvalume® | Galvanized Steel |
Coating Composition | 91% Zn, 6% Al, 3% Mg | 55% Al, 43.5% Zn, 1.5% Si | Nearly 100% Zn |
Corrosion Resistance | Excellent | Good | Fair |
Edge Protection | Excellent self-healing | Moderate self healing | Short-term sacrificial |
Marine/Coastal Use | Excellent (coastal warranties) | Limited (edge rust risk) | Poor |
Formability | High | Moderate | High |
Best Use Cases | Coastal, industrial, ag, premium roofs | General roofing | Budget roofing, indoors |
Looking for More Information on Metal Roofing Materials?
ZAM is a unique balance between the exceptional durability of stainless steel and the cost-effectiveness of other materials like Galvalume. Its corrosion resistance makes it an ideal choice for homes and buildings along the coast or in high-humidity regions. It is becoming more and more popular in the metal roofing world.
Subscribe to the Sheffield Metals Learning Center to check out our related content:
Galvalume® Steel vs. Aluminum: What Metal Roof Material Should I Pick?